The poppets are actuated by cams on a camshaft,
as shown in figure 8-8. They are arranged so that
rotation of the shaft by its controlling lever will open
the proper combination of poppets to direct the flow
of hydraulic fluid to the desired port of the actuating
unit. At the same time, fluid will be directed from the
opposite port of the actuating unit, through the
selector valve, and back to the reservoir.
All poppet-type selector valves are provided with
a stop for the camshaft. The stop is an integral part of
the shaft, and strikes against a stop pin in the body to
prevent overrunning. A poppet selector valve housing
usually contains poppets, poppet seats, poppet
springs, and a camshaft.
When the camshaft is rotated, either clockwise or
counterclockwise from neutral, the cam lobes unseat
the desired poppets and allow a fluid flow. One cam
lobe operates the two pressure poppets, and the other
lobe operates the two return poppets. To stop the
rotation of the camshaft at an exact position, a stop
pin is secured to the body, and extends through a
cutout section of the camshaft flange. This stop pin
prevents overtravel by ensuring that the cam lobes
stop rotating when the poppets have been unseated as
high as they can go, where any further rotation would
allow them to return to their seats.
The poppet-type selector valve has three
positions-neutral and two working positions. In the
neutral position, the camshaft lobes are not contacting
any of the poppets.
This position assures that the
poppet springs will hold all four poppets firmly
seated. With all poppets seated, there is no fluid flow
through the valve. This action also blocks the two
cylinder ports, so when this valve is in neutral, the
fluid in the unit system is trapped. To allow for
thermal expansion buildup, thermal relief valves must
be installed in both working lines.
Figure 8-8.Cutaway view of selector valve body.
8-10
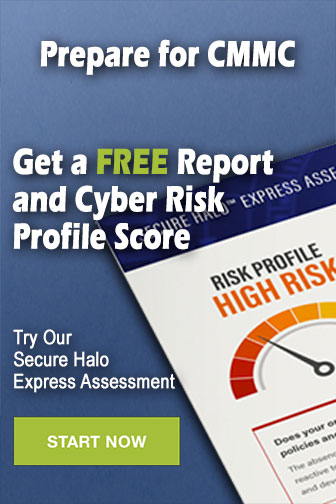