A typical flight control surface actuator is shown
in figure 8-5. This is a tandem-type hydraulic unit,
which means, in this case, that two control valves are
incorporated within a common housing. One of the
control valves is connected to the aircrafts primary
flight control hydraulic system, while the other is
connected to a separate hydraulic system.
This is a typical arrangement since Navy specifi-
cations require two independent hydraulic systems for
operation of the primary flight control systems on all
high-performance aircraft.
Although the two control valves in the actuator
are interconnected mechanically by a synchronizing
rod, they are not interconnected hydraulically. The
purpose of the synchronizing rod is to equalize the
flow of fluid into the actuator piston chambers.
Because the two control valves operate
independently of each other as far as hydraulic
pressure is concerned, failure of either hydraulic
system does not render the actuator inoperative.
Failure of one system does reduce the output force by
one-half; however, this force is sufficient to permit
handling of the aircraft at certain airspeeds (always
well above that required for a safe landing).
This complete actuator consists of the two
isolated piston chambers, a shaft assembly with two
pistons, two end cap assemblies, the two control
valves, and the previously mentioned synchronizing
red.
In this particular installation, the piston shaft end
is attached to the aircraft structure and remains
stationary. The cylinder body is attached to the
control surface, and provides control surface
deflection by its movement. Two adjustable stops are
provided as a means of adjusting actuator movement,
thereby limiting the travel of the control surface.
When these steps are used in an aileron or elevator
control system, one stop limits the UP travel, and the
other limits the DOWN travel. In a rudder system,
one stop limits the travel to the right, and the other to
the left.
MAINTENANCE OF ACTUATING
CYLINDERS
During preventive maintenance inspections, you
inspect actuating cylinders in accordance with the
applicable maintenance requirements cards (MRCs)
for the specific aircraft. Actuating cylinders are
inspected for leakage and binding. You should clean
the exposed portion of the piston shaft with a
dry-cleaning solvent, and then wipe it with a clean
cloth moistened with hydraulic fluid. All mounting
fittings are lubricated with specified grease only.
NOTE: All lubrication fittings and lubri-
cation areas must be cleaned prior to
lubrication, and all excess lubricants must be
removed at its completion.
External leakage is the most common trouble
encountered with actuating cylinders. This can be
caused by static or dynamic seals. Static seal leakage
around end caps or fittings may be stopped by
tightening the affected components or replacing the
leaking seal.
Dynamic seal leakage around an
actuator shaft will require seal replacement. Refer to
the appropriate MIM or 03 manual for specific
maintenance instructions.
WARNING
Applying too much torque while tightening
fittings or other components under
pressure may cause catastrophic failure.
Such failures can result in injury to
personnel or damage to the aircraft.
Internal leakage is harder to detect. This leakage
is usually caused by failure of piston seals, and will
require repair. Internal leakage is usually indicated
by weak, sluggish, or slow movement of the actuator.
Refer to the appropriate MIM or 03 manual for repair
instructions.
This problem is usually resolved by
replacement of the actuator.
After the repairs are
made, you must test the actuator to verify its
performance.
HYDRAULIC MOTORS
Hydraulic motors are used to convert hydraulic
pressure into rotary mechanical motion. The type of
hydraulic motor used in naval aircraft is similar in
general design and construction to the piston-type
pumps. The difference in the operation of a hydraulic
motor and a hydraulic pump is as follows: In the
operation of a pump, when the drive shaft is rotated,
fluid is drawn into one port and forced out the other
under pressure.
This procedure is reversed in a
hydraulic motor.
By directing fluid already under
pressure into one of the ports, pressure will force the
shaft to rotate. Fluid will then pass out the other port,
8-6
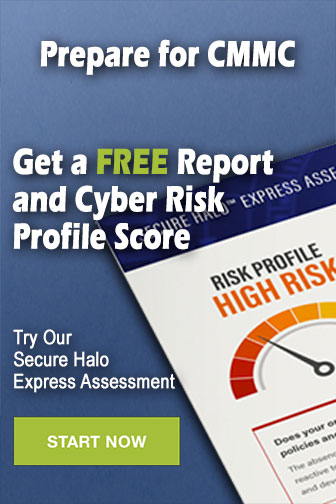