There are many types of valves, such as selector,
pressure reducing, sequence, check, restrictor, and
relief. While the basic function for each type of valve
is similar, the design and construction may be very
different. Examples of these valves are discussed in
the following text.
SELECTOR VALVES
Selector valves are used in a hydraulic system to
direct the flow of fluid. A selector valve directs fluid
under system pressure to the desired working port of
an actuating unit (double-acting), and, at the same
time, directs return fluid from the opposite working
port of the actuating unit to the reservoir.
Some aircraft maintenance instruction manuals
(MIMs) refer to selector valves as control valves. It is
true that selector valves may be placed in this
classification, but you should understand that all
control valves are not selector valves. In the strict
sense of the term, a selector valve is one that is
engaged at the will of the pilot or copilot for the
purpose of directing fluid to the desired actuating
unit. This is not true of all control valves.
Selector valves may be located in the pilots
compartment and be directly engaged manually
through mechanical linkage, or they maybe located in
some part of the aircraft and be engaged by remote
control. Remote-controlled selector valves are
generally solenoid operated.
The typical four-way selector valve has four
portsa pressure port, a return port, and two
cylinder (or working) ports. The pressure port is
connected to the main pressure line from the
power pump, the return port is connected to the
reservoir return line, and the two cylinder ports
are connected to opposite working ports of the
actuating unit.
Three general types of selector valves are
discussed in this chapter. They are the poppet, slide,
and solenoid-operated valves. Practically all selector
valves currently in use come under one of these three
general types.
Poppet-Type Selector Valve
Poppet-type selector valves are manufactured in
both the balanced and unbalanced design. An
unbalanced poppet selector valve offers unequal
working areas on the poppets. The larger area of the
poppet is in contact with the working lines of the
system; consequently, when excessive pressure exists
within the working lines due to thermal expansion, the
poppet will open. This action allows the excessive
pressurized fluid to flow into the pressure line, where
it is relieved by the main system relief valve.
The balanced poppet selector valve has equal
poppet areas. The poppets will remain in the selected
position during thermal expansion of working line
fluid. For this reason, thermal relief valves are
installed in working lines that incorporate balanced
poppet selector valves.
Figure 8-7 shows a typical four-port poppet
selector valve. This is a manually operated valve, and
consists of a group of conventional spring-loaded
poppets. The poppets are enclosed in a common
housing and interconnected by passageways to direct
the flow of fluid in the desired direction.
Figure 8-7.Poppet-type selector valve.
8-9
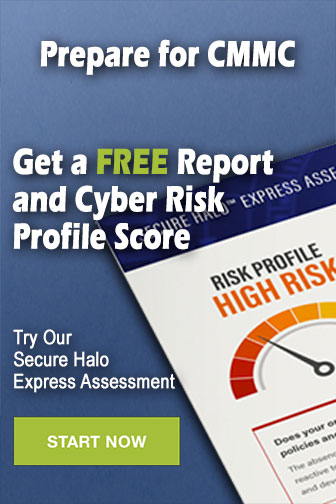