actuating cylinder.
Its purpose is to lock the
down-lock mechanism of the landing gear. The
ball-lock feature is in the lock position when the
landing gear is extended.
The main parts of this cylinder are the body, end
caps, piston shaft and head, ball-lock plunger, locking
ball bearings, ball bearing race, spring guide,
compression spring, and down-lock switch. The
operation of the ball-lock actuator is described in the
following paragraphs.
When the landing gear is down and locked, the
ball-lock actuator will be in the position shown in
view A of figure 8-3. Notice the locking ball bearings
are being held in the ball bearing race detents by the
inner lip of the ball-lock plunger. Since no hydraulic
pressure exists while in this position, the spring-
loaded, ball-lock plunger is held in its retracted
position, allowing the down-lock switch to be
actuated by the groove portion of the piston shaft.
When the landing gear selector valve is
positioned to its retracted (UP) position, pressurized
fluid is allowed to enter the actuator through its only
port. This pressurized fluid forces the ball-lock
plunger to the right, which simultaneously allows the
ball bearings to drop free from their detents in the
bearing race and actuate the down-lock switch, as
shown in view B of figure 8-3. As soon as the locking
ball bearings are released, the piston shaft assembly
retracts, as shown in view C of figure 8-3, and
unlocks the landing gear.
When the landing gear
completes its UP cycle, the selector valve returns to
neutral, trapping hydraulic fluid within the actuator
until the next cycle begins.
FINGER-LOCK ACTUATOR.The actuating
cylinder shown in figure 8-4 is a double-action,
two-port, finger-lock, balanced actuator. This type of
actuator is currently installed as a main landing gear
component on some aircraft. It incorporates an inner
cylinder to equalize the displacement of fluid on
either side of the piston.
As shown in view A of figure 8-4, an integral,
finger-type, spring-loaded, mechanical lock is also
incorporated within the actuator to lock the piston
shaft assembly in the extended position.
The
finger-lock actuator has a down-limit switch mounted
on and through the cylinder area, which indicates
when the landing gear is down and locked; also, an
added feature that is common on landing gear
actuators is an integral shuttle valve. The shuttle
valve allows connection of both the normal extension
hydraulic fluid line and the emergency pneumatic
extension pressure line. The operation of the
finger-lock actuator is described in the following
paragraphs.
When the pilot positions the selector valve in the
landing gear retracted position, view A of figure 8-4,
hydraulic pressure is directed to the cylinders retract
port.
Hydraulic pressure entering the cylinder
overcomes piston spring force, which permits the
locking fingers to open as the piston shaft assembly is
retracted into the cylinder.
During normal extension of the landing gear
(view B of figure 8-4), hydraulic pressure is directed
from the selector valve to the normal extension port of
the integral shuttle valve. This pressurized fluid
forces the piston towards the extended position. As
the piston comes in contact with the locking fingers,
hydraulic pressure and spring tension are required to
force the piston over the fingers while fully extending
the piston shaft assembly. At the same time the piston
is being forced over the locking fingers, it contacts the
cam-shaped lower end of a toggle shaft, which
extends radially into the cylinder area, thereby
rotating the shaft. Movement of the toggle shaft is
transmitted to the main landing gear down-limit
switch, which is attached to the outer surface of the
cylinder. This indicates the cylinder is in the locked
position.
Control Surface Actuating Cylinder
Actuators are used in conjunction with power-
operated flight control systems. Their function is to
assist the pilot in handling the aircraft, in the same
way as power steering aids in handling an automobile.
In a power-operated flight control system, all the
force necessary for deflecting the control surface is
supplied by hydraulic pressure.
Each movable
surface is operated by a hydraulic actuator
incorporated in the control linkage. Some aircraft
manufacturers refer to these units as power control
cylinders; however, all flight control system actuators
and power control cylinders perform the same
function, and are similar in principle of operation.
8-4
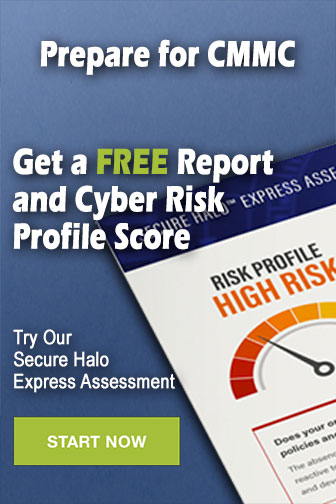