CHAPTER 8
BASIC ACTUATING SYSTEMS
Chapter Objective: Upon completion of this chapter,
knowledge of the components of the basic actuating
maintenance procedures.
The actuating systems consist of the hydraulic
components used to direct and control the flow of
pressurized fluid as well as the components used to
perform the actual work. This chapter begins with a
discussion of actuating units, and covers most of the
various actuating system components that are used in
modern-day hydraulic systems.
ACTUATING UNITS
Learning Objective: Identify various
hydraulic actuating units.
An actuating unit may be defined as a unit that
transforms hydraulic fluid pressure into mechanical
force, which performs work (moving some
mechanism). Two types of actuating units are used in
naval aircraftactuating cylinders and hydraulic
motors. Both types are discussed in this chapter.
TYPES OF ACTUATING CYLINDERS
Actuating cylinders are the most commonly used
actuating units in aircraft hydraulic systems. The
purpose of an actuating cylinder is to convert fluid
under pressure into linear or mechanical motion.
Actuating cylinders are generally installed in such a
manner that the piston shaft (rod) end of the cylinder
is attached to the mechanism to be actuated, with the
other end attached to the aircraft structure.
There are two types of actuating cylinders
balanced or unbalanced. Balanced actuators have
equal working areas, with a piston shaft extending
from both sides of the piston head. This type of
cylinder may be a single-acting actuator, which
receives hydraulic pressure on only one side of the
piston head for movement in one direction, and some
other means of force for movement in the opposite
direction. However, it may also be a double-acting
type, which uses hydraulic pressure alternately on
you will have a working
systems and their related
both sides of the piston head to move it in the selected
direction.
The most common type of actuating cylinder used
on naval aircraft is the unbalanced type, which maybe
either single or double acting. Unlike the balanced
actuator, it has a single piston shaft extending from
the piston head, resulting in unequal working areas.
Each actuator used may differ considerably in size
and construction.
Single-Acting Actuating Cylinder
The single-acting, piston-type cylinder uses fluid
pressure to apply force in only one direction. In some
designs of this type, the force of gravity moves the
piston in the opposite direction. However, most
cylinders of this type apply force in both directions.
Fluid pressure provides the force in one direction, and
spring tension provides the force in the opposite
direction, In some single-acting cylinders, com-
pressed air or nitrogen is used instead of a spring for
movement in the direction opposite that achieved with
fluid pressure.
Figure 8-1 shows a single-acting, spring-loaded,
piston-type actuating cylinder. In this cylinder the
spring is located on the rod side of the piston. In some
spring-loaded cylinders, the spring is located on the
blank side, and the fluid port is located on the rod side
of the cylinder.
Figure 8-1.Single-acting, spring-loaded, piston-type
actuating cylinder.
8-1
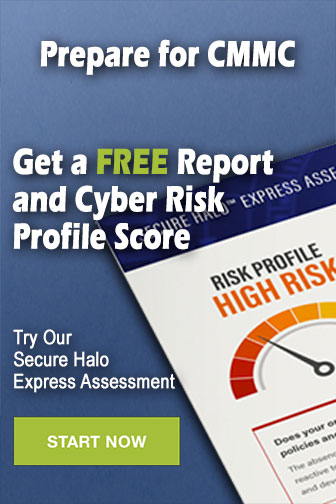