The other type of system in current use has its
own compressor and other equipment necessary for
maintaining an adequate supply of compressed air
during flight. Provision for ground charging this type
of system is also provided. In addition to a
compressor, the components in this type of system
usually include a filter, a pressure regulator, a
moisture separator, a relief valve, a chemical drier,
and storage cylinder(s).
AIR COMPRESSORS.A typical air com-
pressor is shown in figure 7-43. An installation of this
type receives its supply of air from the compressor
section of the aircraft engine.
This air is then
compressed further to the required pressure for
operating the system. Compressors of this type are
capable of maintaining up to and above 3,000 psi
pressure during flight.
On some aircraft, the compressor is operated by
an electric motor. On others, a hydraulic motor is
used to drive the compressor. Compressors must be
serviced with oil periodically, as outlined in the
aircraft MIM. An oil level sight gauge is provided on
the compressor (fig. 7-43).
AIR FILTERS.An air filter is usually located
in the line leading into the system compressor.
Additional filters may be located at various points in
the system lines to remove any foreign matter that
may enter the system.
Figure 7-43.Air compressor.
Like hydraulic filters, air filters have a removable
element and a built-in relief valve. The relief valve is
designed to open and bypass the air supply around the
filter element should the element become clogged.
Some air filters are equipped with the micronic-type
element, which must be replaced periodically. Others
have the screen mesh type, which requires periodic
cleaning. The latter type may be reinstalled after
cleaning and drying.
AIR PRESSURE REGULATORS.A pressure
regulator is generally located in the line between the
engine compressor and the pneumatic system
compressor; however, it may be incorporated within
the system moisture separator. Its purpose is to
regulate the pressure of the supply air before it enters
the system compressor. The pressure regulator
maintains a stable outlet pressure regardless of the
inlet pressure.
MOISTURE SEPARATORS.The moisture
separator in a pneumatic system is always located
downstream of the compressor. Its purpose is to
remove any moisture caused by the compressor. A
complete moisture separator consists of a reservoir, a
pressure switch, a dump valve, and a check valve, and
it may also include a regulator and a relief valve. The
dump valve is energized and de-energized by the
pressure switch. When de-energized, it completely
purges the separator reservoir and lines up to the
compressor.
The check valve protects the system
against pressure loss during the dumping cycle and
prevents reverse flow through the separator.
RELIEF VALVES.A relief valve is
incorporated in a pneumatic system to protect the
system from overpressurization. Overpressurization
is generally caused by thermal expansion (heat).
Relief valves are generally adjusted to open and close
at pressures slightly above normal system operating
pressure.
For example, in a system designed to
operate at 3,000 psi, the relief valve might be set to
open at 3,750 psi and reseat at 3,250 psi.
CHEMICAL DRIERS.Chemical driers are
incorporated at various locations in a pneumatic
system. Their purpose is to absorb any moisture that
may collect in the lines and other parts of the system.
Each drier contains a cartridge, which should be
blue in color. If otherwise noted, the cartridge is to be
considered contaminated with moisture and should be
replaced.
STORAGE CYLINDERS.Pneumatic storage
cylinders (bottles) are made of steel and maybe either
7-44
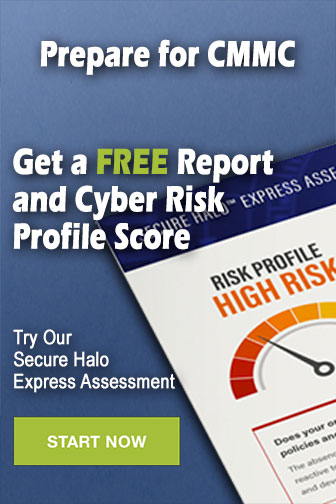