EMERGENCY SYSTEMS
According to the military specifications discussed
earlier in this chapter, an aircraft may have a standby
hydraulic system for emergency operation of the
flight controls, a compressed air (pneumatic) system
for operating the brakes, and a mechanically operated
system for lowering the landing gear. Inspection and
maintenance of these systems are also your
responsibility.
On aircraft using a standby hydraulic system, the
emergency power system components will usually
include a reservoir, a pump, and an emergency control
in the cockpit for switching from NORMAL to
EMERGENCY. Additional components will vary
from aircraft to aircraft, depending on the method
used for driving the emergency pump.
The emergency system pump may be
electric-motor driven, ram-air turbine driven, or it
may be hand operated. All three methods are
currently used on naval aircraft.
Regardless of the method used in driving the
pump, the emergency power system must be
completely independent of the normal power system.
The normal and emergency lines are usually separated
as far apart from each other as practicable. This is
done to reduce to a minimum the possibility of both
lines being ruptured by a single projectile.
The emergency reservoir is usually located as
remotely as practicable from the normal reservoir, but
it is generally possible to fill both reservoirs through a
common filler port. Usually, the filler port is located
on the normal system reservoir.
Operation of Typical Motor-Driven System
A schematic diagram of a typical electric
motor-driven emergency power system is shown in
figure 7-40. Individual components included in the
system are a reservoir, a motor-driven pump, an
accumulator, a relief valve, a pressure switch, a
snubber, and a control switch in the cockpit.
The main difference in a system of this type and a
normal (engine-driven) system is that instead of
operating continuously, the pump operates only when
pressure is needed in the system. For example, if the
normal power system is inoperative, the pilot turns on
the emergency system switch in the cockpit. Turning
this switch on energizes a pressure switch that is
connected into the emergency hydraulic system
pressure line.
The pressure switch is actuated
automatically by hydraulic pressure.
For example, when emergency system pressure
drops below a predetermined point, the pressure
switch turns the pump motor on. When the pressure
builds up to the designed operating psi, the pressure
switch turns the pump motor off.
The system is protected from excessive pressures
by a relief valve, which is set to open at a pressure
slightly above system operating pressure. Emergency
power systems of this type are generally equipped
with an accumulator for storing a reservoir supply of
fluid under pressure. This prevents the pump motor
from having to cut in repeatedly to maintain operating
pressure in the system.
Ram Air Turbine-Driven System
In this type of emergency hydraulic system, ram
air is used to turn the blades of a turbine that, in turn,
operates a hydraulic pump. The turbine and pump
assembly is generally installed on the inner surface of
a door installed in the fuselage. The door is hinged,
allowing the assembly to be extended into the
slipstream by pulling a manual release in the cockpit.
Figure 7-40.Schematic diagram of typical emergency power
system (electric-motor driven).
7-41
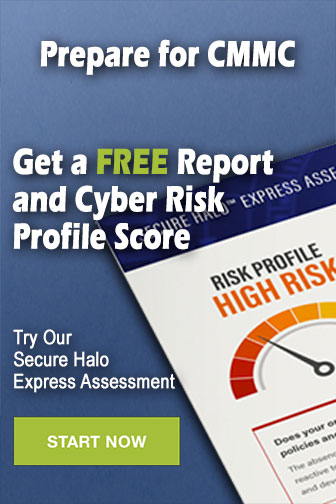