element must be carefully handled to protect it from
contamination and mechanical damage.
5. The replacement element is installed in
reverse order of its removal. In most instances the
element is inserted up into the head, employing a
gentle twisting motion. O-ring seals located in the
head, or sometimes in the element itself, prevent fluid
from flowing around the element. It is important that
these seals be inspected and replaced, if required, in
accordance with the applicable MIM.
6. Prior to installation of the cleaned filter bowl,
the bowl is first filled with new filtered hydraulic
fluid to minimize the introduction of air into the
hydraulic system. It is important that the fluid used
for this operation be obtained only from an authorized
hydraulic fill service unit.
7. Once filled, the filter bowl is carefully and
slowly slid up over the installed element and screwed
into the head. A quantity of fluid from the bowl will
normally be displaced by the element and spilled.
Provisions must be made to collect or absorb it.
8. The installed filter bowl should be torqued to
the value specified in the applicable MIM. The bowl
is then lockwired, using standard tools and the
lockwire provisions in the filter assembly.
9. All filter element installations should be
followed by test and inspection of the system to
ensure proper operation.
This is generally
accomplished by operating the system at its normal
pressure and flow rates and inspecting for external
leakage at the filter assembly and for indications of
excessive differential pressure. Any external leakage
is unacceptable, and requires that the system be shut
down and the problem corrected.
10. Should the filter assembly differential
pressure indicator continue to extend after a new
element has been installed, the indicator itself is
probably defective.
Consult the maintenance
instructions to determine what corrective action is to
be taken.
Inspect the filter element as follows:
1. Visually inspect the element for dents, broken
wires, holes, creases, and sharp corners of pleats.
Permissible damage is to be confined to small dents
that will not impede the required flow, or increase the
filter pressure drop beyond tolerance, or fail to pass
the required bubble test point. Deeper dents, broken
wires, holes, creases, and sharp corners of pleats are
cause for rejection of elements.
2. Remove the O-ring from the filter element and
visually inspect the O-ring groove, including
chamfers, for nicks, dents, visible roughness,
out-of-roundness, and pitting. Blend out nicks and/or
scratches that are deeper than 0.002 inch with crocus
cloth P-C-458.
3. Visually inspect mating surfaces, including
chamfers, or other parts that mate with the O-ring
grooves. Make sure that all surfaces (grooves and
mating surfaces) are smooth and capable of sealing
with the O-ring installed.
4. Dispose of unacceptable filter elements
according to existing instructions.
ACCUMULATORS
The purpose of the accumulator in a hydraulic
system is to store a volume of fluid under pressure.
There are several reasons why it is advantageous to
store a volume of fluid under pressure. Some of these
are listed below:
1. An accumulator acts as a cushion against
pressure surges that may be caused by the pulsating
fluid delivery from the pump or from system
operations.
2. The accumulator supplements the pumps
output when the pump is under a peak load by storing
energy in the form of fluid under pressure.
3. The energy stored in the accumulator may be
used to actuate a unit in the event of normal hydraulic
system failure. For example, sufficient energy can be
stored in the accumulator for several applications of
the wheel brakes.
There are two general types of accumulators in
use on naval aircraft. They are the spherical type and
the cylindrical type.
Until a few years ago, the
spherical type was the more commonly used
accumulator; however, the cylindrical type has proved
more satisfactory for high-pressure hydraulic
systems, and is now more commonly used than the
spherical type. Examples of both types are shown in
figure 7-34.
Spherical Type
The spherical type accumulator is constructed in
two halves that are screwed together. A synthetic
rubber diaphragm is installed between both halves,
making two chambers. Two threaded openings exist
7-36
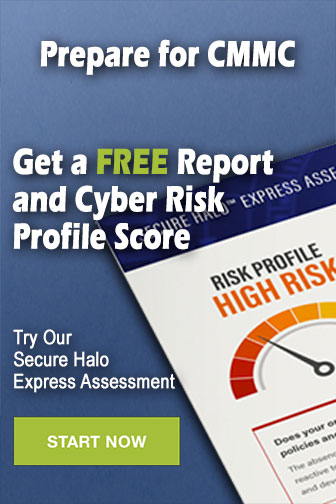