piston downward, breaking the magnetic attachment
between the indicator button and the magnetic piston.
This allows the red indicator to pop out, signifying
that the element must be cleaned. The button or pin,
once extended, remains in that position until manually
reset and provides a permanent (until reset) warning
of a loaded element. This feature is particularly
useful where it is impossible for an operator to
continuously monitor the visual indicator, such as in
an aircraft. Some button indicators have a thermal
lockout device incorporated in their design that
prevents operation of the indicator below a certain
temperature.
The lockout prevents the higher
differential pressure generated at cold temperatures
by high fluid viscosity from causing a false indication
of a loaded filter element.
Differential pressure indicators are a component
part of the filter assembly in which they are installed,
and, as such, are normally tested and overhauled as
part of the complete assembly. With some model
filter assemblies, however, it is possible to replace the
indicator itself, without removal of the filter
assembly, if it is suspected of being inoperative or out
of calibration.
It is important that the external
surfaces of button-type indicators be kept free of dirt
or paint to ensure free movement of the button.
Indications of excessive differential pressure,
regardless of the type of indicator employed, should
never be disregarded. All such indications must be
verified and action taken, as required, to replace the
loaded filter element. Failure to replace a loaded
element can result in system starvation, filter element
collapse, or the loss of filtration where bypass
assemblies are used. Verification of loaded filter
indications is particularly important with button-type
indicators, as they may have been falsely triggered by
mechanical shock, vibration, or cold start of the
system. Verification is usually obtained by manually
resetting the indicator and operating the system to
create a maximum flow demand, ensuring that the
fluid is at near normal operating temperatures.
Maintenance
Hydraulic filter maintenance consists of filter
element replacement only. You must be familiar with
both replacement and general inspection procedures.
Replacement of hydraulic filter elements is
normally a maintenance operation performed on a
periodic basis, but need for prior replacement may be
indicated during routine inspection. Hydraulic filter
assemblies in some aircraft and SE are equipped with
indicating devices (buttons or pins) that will extend
when the differential pressure across the filter
exceeds a predetermined value, indicating a loaded
element.
Upon appearance of this indicator, it
becomes necessary to verify the condition of the filter
element, and replace it if required. When checking or
changing filter elements, also check the functioning
of any pop-up mechanism.
Indications of a loaded filter must be verified to
confirm that release of the button or pin is due to a
loaded filter and not a result of system mechanical
shock or cold start. Verification is accomplished by
resetting the indicator (manually depressing it) and
operating the system at full power. If the differential
pressure indicator extends again during this test, the
filter element should be replaced.
It is important that the applicable MIM be
consulted for specific filter element replacement
procedures. The following basic principles apply to
most replacement operations:
1. Removal of the filter bowl is the first step in
replacing the filter element. With most filter
assemblies, this operation usually consists of
removing a lockwire and unscrewing the bowl from
the filter head. In most filter assemblies, an automatic
shutoff valve in the head will prevent fluid loss from
the system when the bowl is removed.
2. Once the bowl is removed, the fluid in it is
discarded, and the bowl is cleaned of sediment by
flushing with clean, unused hydraulic fluid or dry
cleaning solvent, P-D-680. It is important that
chlorinated solvents such as MIL-C-81302 or
1,1,1-trichloroethane are not used, as their residues
may have harmful effect on the system.
3. The filter element is, in most instances,
removed from the head by a gentle twisting and
pulling motion.
Once removed, the surface of the
element should be visually inspected. An excessive
amount of particulate on its surface, as determined
from experience, may be indicative of upstream
component failure and the need for investigation.
Check the solid end of filter element for Disposable
markings. If the filter element is disposable, it should
be discarded. If the filter element is not disposable, it
should be cleaned and handled carefully.
4. The replacement filter element should not be
removed from its protective packing until just prior to
installation. Once removed from packing, the
7-35
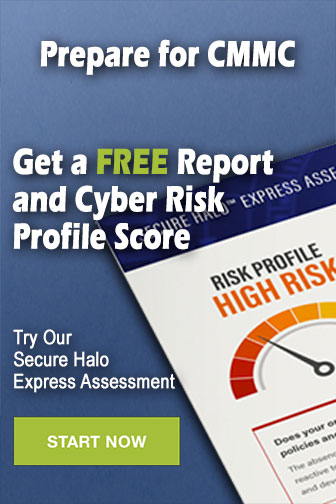