in the assembled component. The opening at the top,
as shown in figure 7-34, contains a screen disc that
prevents the diaphragm from extruding through the
threaded opening when system pressure is depleted,
thus rupturing the diaphragm. On some designs the
screen is replaced by a button protector fastened to the
center of the diaphragm. The top threaded opening
provides a means for connection of the fluid chamber
of the accumulator to the hydraulic system.
The bottom threaded opening provides a means
for installation of an air filler valve. This valve (when
open) allows an air/nitrogen source to be connected to
and enter the accumulator; moreover, when the valve
is closed, it traps the air/nitrogen within the
accumulator.
Figure 7-34.Pressure accumulator, spherical and cylindrical
types.
Cylindrical Type
Cylindrical accumulators consist of a cylinder
and piston assembly. End caps are attached to both
ends of the cylinder. The internal piston separates the
fluid and air/nitrogen chambers. Both the end caps
and piston are sealed with gaskets and packings to
prevent external leakage around the end caps and
internal leakage between the chambers. In one end
cap, a hydraulic fitting is used to attach the fluid
chamber to the hydraulic system. In the other end
cap, an air filler valve is installed to perform the same
function as the filler valve installed in the spherical
accumulator.
Operation
In operation, the compressed-air chamber is
charged to a predetermined pressure, which is
somewhat lower than the system operating pressure.
This initial charge is referred to as the accumulator
preload.
As an example of accumulator operation, let us
assume that the cylindrical accumulator in figure 7-34
is designed for a preload of 1,300 psi in a 3,000 psi
system. When the initial charge of 1,300 psi is
introduced into the unit, hydraulic system pressure is
zero. As air pressure is applied through the air
pressure port, it moves the piston toward the opposite
end until it bottoms. If the air behind the piston has a
pressure of 1,300 psi, the hydraulic system pump will
have to create a pressure within the system greater
than 1,300 psi before the hydraulic fluid can actuate
the piston. Thus, at 1,301 psi the piston will start to
move within the cylinder, compressing the air as it
moves. At 2,000 psi it will have backed up several
inches. At 3,000 psi the piston will have backed up to
its normal operating position, compressing the air
until it occupies a space less than one-half the length
of the cylinder.
When actuation of hydraulic units lowers the
system pressure, the compressed air will expand
against the piston, forcing fluid from the accumulator.
This supplies an instantaneous supply of fluid to the
hydraulic system.
Many aircraft have several accumulators in the
hydraulic system.
There may be a main system
accumulator and an emergency system accumulator.
There may also be auxiliary accumulators located in
various unit systems. Regardless of the number and
their location within the system, all accumulators
7-37
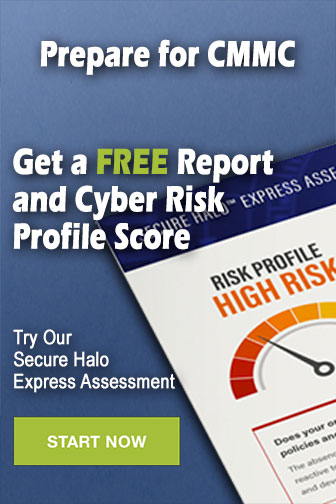