Slide-Type Selector Valve
The slide-type selector valve is probably the most
durable and trouble-free valve currently in use. Some
manufacturers refer to this type valve as a piston or
spool type. Figure 8-10 shows a cutaway view of a
typical four-port slide-type selector valve. The main
parts of the valve consist of a body, sleeve, slide, detent
springs, and the necessary packings and gaskets.
The valve body is cast aluminum alloy. It has
four fluid portspressure, return, and two cylinder
ports.
A large bore has been drilled lengthwise
through the body, and all four fluid ports connect into
this main bore at intervals along its length. There is
also a drilled passageway in the body that runs
alongside the main bore. This passageway is used to
connect one of the cylinder ports to the return port.
A hollow steel sleeve (3) tits into the main bore of
the body. Around the outside diameter of the sleeve are
six O-ring gaskets.
As the sleeve is inserted into the
main bore, these O-rings form a seal between the sleeve
and the body. This creates five chambers around the
sleeve, and each chamber is formed by two of the O-ring
gaskets. Each one of these chambers is lined up with
one of the fluid ports in the body. The drilled
passageway in the body accounts for the fifth chamber,
which results in having the two outboard chambers
connected to the return port. The sleeve has a pattern of
holes drilled through it to allow fluid to flow from one
port to another.
A series of holes are drilled into the
hollow center of the sleeve between each O-ring gasket.
A steel slide (5) or spool is machined so the
largest diameter portions have a close tolerance fit in
the sleeve. Typically, the slide has three raised,
machined portions known as land areas. These areas
usually have several grooves machined into them
around the circumference, breaking each area into
several lands. The lands (and grooves), in concert
with the close machined tolerances, provide for easy,
smooth operation, long service, and no leakage.
One end of the slide is connected to the control
handle in the cockpit through mechanical linkage.
When the control handle is moved, it will then
position the slide within the sleeve. The slide lands
then line up different combinations of fluid ports,
thereby directing a flow of fluid through the valve.
On the end of the slide, next to the eye, are three
grooves called detents. These detents are used to
leek the slide in the exact position needed to properly
direct the fluid flow.
The detent spring (6) is a clothespin-type spring,
secured to the end of the body by a spring retaining bolt
(7). The two legs of the spring extend down through
slots in the sleeve and fit into the detents. The slide is
gripped between the two legs of the spring. To move the
slide, enough force must be applied to spread the two
spring legs and allow them to snap back into the next
detent, which is another position.
Because of the very close fit between the slide
and sleeve, the most common cause of failure or
malfunction is the presence of dirt or foreign matter.
Foreign matter could result in binding of the slide,
scratching the machined surface, and damage to
O-rings. Originally, these valves were provided with
protective boots on both ends of the slide to prevent
dirt or corrosion from getting on the exposed
machined surface, where it would be carried into the
valve when the slide was moved. These protective
boots usually are missing on valves currently issued,
leaving the machined surface exposed. As a
preventive measure, in place of the boots, a light film
of hydraulic fluid should be applied to the exposed
areas of the slide. Primarily, this oil film is to prevent
corrosion, but it helps to prevent any entry of foreign
matter into the valve. Proper linkage adjustment is
necessary because linkage that is too long or too short
will prevent the detent spring from locking the slide in
the correct position.
If it becomes necessary to test this valve under
pressure to determine the cause of malfunction, it is
important to first check the MIM for the particular
installation. A slight amount of internal leakage is
permitted in the working positions, and this should
not be mistaken for faulty operation.
Solenoid-Operated Selector Valve
A solenoid-operated selector valve is an
electrically controlled valve. Solenoid-operated
selector valves may be either the slide type or the
poppet type.
They differ from the manually
controlled valves previously described in that they are
electrically controlled by one or more solenoids
contained within the valve.
A solenoid may be defined as a hollow or
tubular-shaped electric coil, made up of many turns of
fine insulated wire, that possesses the same properties
as an electromagnet. The hollow core imparts linear
motion to a movable iron core (or plunger) placed
within the hollow core of the solenoid.
8-12
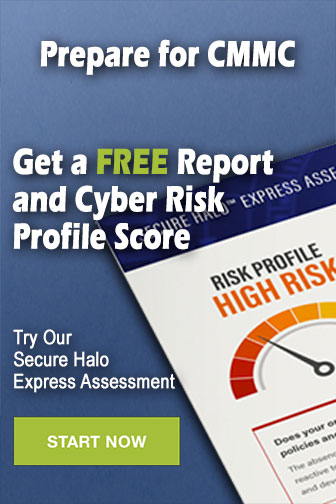