the master cylinder. Power brake systems use utility or
main hydraulic system pressure from the aircraft. The
power brake systems allow for higher brake line
pressures than can be obtained with the independent
system.
INDEPENDENT-TYPE BRAKE SYSTEM
The depth of independent brake system mainte-
nance allowable at the intermediate and organizational
levels of maintenance varies with the complexity of the
components. System maintenance at the organizational
level generally consists of servicing, troubleshooting,
parts replacement, and on aircraft repairs. Bleeding of
the brake system is discussed later in this chapter.
Reservoir maintenance is limited to servicing,
removal, repair, parts replacement, testing, and
installation. Servicing of the reservoir requires that
filtered hydraulic fluid be gravity fed into the reservoir
through the filler opening until the sight gauge indicates
it is full. The reservoir should not be overfilled. The area
around the filler neck should be cleaned before you
remove the filler plug to prevent any form of
contamination from being introduced into the reservoir
and the brake system. Maintenance of the reservoir, the
master brake cylinder, and the brake assembly is
discussed later in this chapter.
As with other systems, a troubleshooting chart is fur
nished in the MIM for use in troubleshooting/ analyzing
main landing gear wheel and independent brake system
malfunctions. Chapter 3 of this training manual contains
examples of troubleshooting tables and charts.
POWER-TYPE BRAKE SYSTEM
Organizational maintenance of the power/manual
brake system consists of checking system operation,
system adjustment, isolating malfunctions, and
replacement and adjustment of system components. See
figure 12-35. The checkout procedures in most MIMs
are provided for use during established inspections or
for use in performing trouble analysis.
GENERAL BRAKE SYSTEM
MAINTENANCE
Proper functioning of the brake system is of the
utmost importance. Inspections must be performed at
frequent intervals, and maintenance work must be
performed promptly and carefully.
Operational Checks
Prepare the aircraft for an operational checkout by
installing the landing gear down locks, jacking the
aircraft to provide proper ground clearance for the
landing gear, and applying external electrical power.
Placing the antiskid switch in the OFF position should
illuminate the antiskid warning light. When the landing
gear handle is moved to the UP position, the antiskid
light should go out. At this point, external hydraulic
power is slowly applied to the utility system. The wheels
should not rotate. By placing the landing gear handle to
the DOWN position, it should illuminate the antiskid
light and free the wheels to rotate. The brake pedals
should be fully depressed to apply the brakes a minimum
of three times.
With external hydraulic and electrical power
removed from the aircraft, operationally check the
emergency system by pulling the emergency brake
handle. The wheels should not rotate when the handle is
pulled. Releasing the handle should immediately release
the brakes. If any portion of the operational or functional
test does not meet the results specified in the MIMs,
refer to the trouble analysis sheets for the brake system.
Functional Tests
Prepare the aircraft for a complete functional
checkout by installing the landing gear down locks,
jacking the aircraft to provide ground clearance for the
landing gear, installing pressure gauges in the wheel
brake assembl ys bleed ports, and applying external
electrical and hydraulic power.
When the antiskid switch is in the OFF position, the
antiskid warning light will illuminate. Move the landing
gear handle to the UP position, which will cause the
antiskid warning light to go out. The gauges on the brake
assemblies should indicate 650 to 1,000 psi. Place the
landing gear handle to the DOWN position to illuminate
the antiskid warning light. The brake gauges should
indicate a maximum of 75 psi, and the wheels should be
free to rotate.
Remove electrical power from the aircraft. Depress
the brake pedals several times to check braking action.
Place a bubble protractor on the brake pedals and adjust
to zero when the brakes are in the OFF position. When
the brakes are fully depressed, the protractor should
indicate 30 degrees ±1 degree, and the hydraulic gauges
on the brake assemblies should indicate the same
pressure as the external hydraulic power source.
The external hydraulic power is shut down and
system pressure is relieved by operating the rudder
pedals. Check brake accumulator action by fully
depressing the brake pedals several times and checking
the brake assembly action. Check the emergency brake
system in the same manner as described for the
operational checkout.
12-41
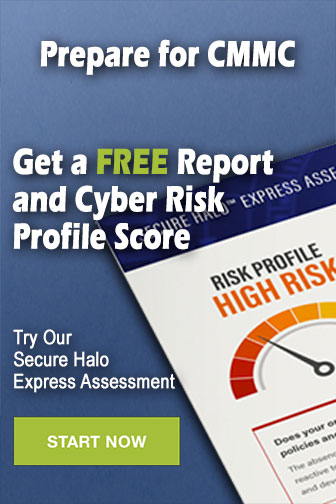