and retainer; a new filter, packing, and plug; and a new
nameplate for the reservoir housing.
Clean the reservoir inside and out with P-D-680
cleaning solvent. Use a fiber brush on threads. Dry the
interior with clean, dry compressed air from a regulated
low-pressure source.
After the reservoir is cleaned and the cure-date
repair kit parts have been installed, conduct a leakage
test. This is accomplished by connecting a source of
25-psi air to the filler port and applying pressure. The
reservoir should then be submerged in a tank of water
for a minimum of 2 minutes. No leakage should be seen.
POWER BRAKE VALVE
Maintenance of these valves at organizational-level
activities is limited to removal and replacement. After
installation, rig the valves. Make an operational check
of the brake system in accordance with the MIMs.
Repair of the brake control valve consists of
disassembly, cleaning, inspection, reassembly, and
testing.
Disassembly
Perform the disassembly in a clean working area.
As you remove parts, place them in a clean container for
protection against dirt and damage. If the valve is to be
disassembled for a considerable length of time, the parts
should be protected from moisture. Note the method of
lockwiring for reference during the reassembly process.
Remove the end cap and the plunger assembly as a unit.
Disassemble the end cap and plunger assembly for
inspection, cleaning, and replacement of sealing
devices. Remove the opposite end cap and remove the
slide and sleeve assembly as a unit for disassembly.
Cleaning
Use P-D-680 cleaning solvent to clean parts. Except
for the slide and sleeve, remove stubborn accumulations
of dirt with a stiff bristle nonmetallic brush moistened
in cleaning solvent. Dry all parts with low-pressure, dry,
filtered air.
NOTE: The slide and the sleeve assembly are
precision lapped parts; they must be kept
together as a matched set. You should take extra
care to prevent damage during maintenance.
Inspection
Using a strong light and preferably some
magnification, inspect all parts for scoring, nicks,
cracks, burrs, excessive wear, corrosion, or damage.
Carefully examine all packing grooves and lands for
burrs and damage. The chrome plating of the plunger
should be inspected for blisters, pinholes, flaking, or
damage, and plating should be continuous. The sliding
surfaces of the slide and sleeve should be free from
scratches, burrs, or nicks. Inspect the seating edges of
the slide for sharpness and freedom from nicks and
burrs. Any damage to the slide and sleeve will
necessitate replacement of both parts of the matched
assembly. The holes in the valve-actuating lever are
checked for elongation, and the roller that makes contact
with the plunger is checked for smoothness and freedom
from nicks and flat spots. Test springs for free length
and test length versus test load in accordance with the
spring data table provided in the 03 manual.
Reassembly
Before reassembly, immerse all internal parts in
filtered, clean hydraulic fluid. Parts are reassembled
while they are still wet. Reassembly is accomplished in
the reverse order of disassembly. Upon completion of
reassembly, adjust the lever backstop adjustment screw
to the dimensions indicated in figure 12-42.
Testing
Figure 12-42 shows the operational test setup used
to accomplish the variety of tests required to verify that
the valve is ready for issue. A test stand capable of
supplying hydraulic pressure from 0 to 4,500 psig
pressure is required. Air is bled from the valve, and
testing is conducted in accordance with the test
procedures table provided in the MIMs and/or 03
manual. Tests include proof test, static pressure test,
pressure drop test for internal leakage, and a complete
operational test to verify power operation and
adjustment. A test troubleshooting table can be found in
the "Intermediate Repair section of most MIMs and 03
manuals. Tables may be used to assist in isolating causes
for malfunctions that result from repair action.
After testing, fill the valve with preservative
hydraulic fluid and plug all ports. Lockwire the lever
backstop adjustment screw, the plunger end cap, and the
end plug in the manner recorded before disassembly.
12-46
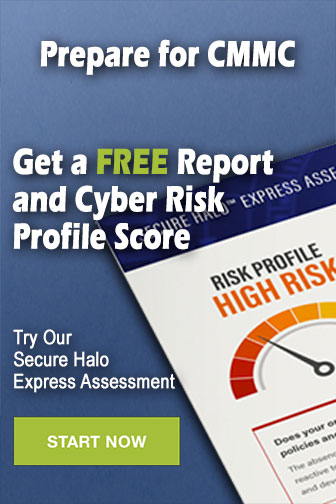