Figure 12-42.Operational test setuppower brake valve.
POWER/MANUAL BRAKE VALVE
There is no daily or routine maintenance required
on the power/manual brake valve other than a wipe
down of the exposed portion of the rod. There are,
however, certain repairs that can be effected in case of
valve malfunction. These include replacement of seals,
as required, tube, shaft, springs, or even the body in
more serious cases.
Tests are not required on the individual valve parts.
After disassembly, cleaning, inspection, repair or
replacement, lubrication, and complete reassembly have
been accomplished, perform a bench test. This test will
determine whether the unit satisfies the required
minimum specifications.
Test the power/manual brake valves on a test bench
before installation in the aircraft. The test bench must be
capable of supplying hydraulic fluid filtered through a
3-micron filter at a maximum pressure of 2,250 psi.
During the test the room temperature should be 70° to
90°F, and the fluid temperature 70° to 110°F.
The bench test is divided into the manual section
and the power section. No particular sequence of
performance of bench test is required, except that the
proof pressure test of a section must precede the leakage
test of that section. Bleed all air from the unit before it
is tested.
Proof Pressure Test-Manual Section
For this test the valve shaft must be harnessed in the
midposition (1-inch plunger stroke), and the RETURN
port must be plugged. Apply hydraulic pressure of 2,250
psi to the BRAKE port. There should be no evidence of
external leakage, permanent distortion, failure, or
malfunction of any part of the valve.
PUMPING TEST.To perform the pumping test,
you should connect a reservoir to the RETURN port by
means of a 3/8-inch ID hose that is at least 24 inches
long. Position the reservoir in such a way that the fluid
is above (but not more than 6 inches) the RETURN port.
Move the shaft to the fully actuated (2-inch plunger
stroke) position, and then cap the BRAKE port.
To perform the pumping test, cycle the valve
rapidly. A rapid decrease in the length of successive
pressure strokes should be noted. On each cycle the
return stroke should be self-motivated.
LEAKAGE TEST.Reposition the unit on the
bench and harness the valve shaft in the midposition.
With the RETURN and PRESSURE ports open,
hydraulic pressure of 25 psi should be applied to the
BRAKE port. There should be no evidence of external
leakage, failure, or malfunction of any part of the valve.
After the first minute, leakage at the RETURN port
should not exceed 1 cubic centimeter per minute for 2
minutes. If satisfactory at this stage, repeat the
procedure by using 500 psi at the BRAKE port.
With the valve in the relaxed position, apply static
hydraulic pressure of 5 psi to the BRAKE and RETURN
ports. There should be no external leakage, failure, or
malfunction of any part of the valve. Repeat the
procedure with 200 psi of static hydraulic pressure.
Proof Pressure Test-Power Section
A pressure of 2,250 psi should be applied to the
PRESSURE port with the BRAKE and RETURN ports
open. Maintain the pressure for 2 minutes, and then look
12-47
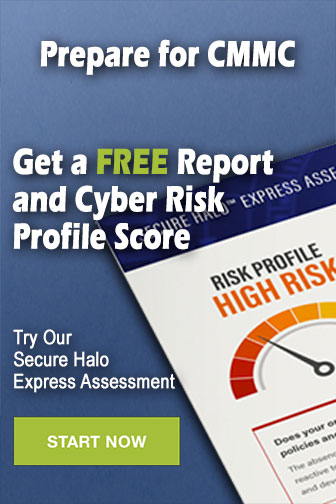