for evidence of external leakage, failure, or permanent
set. Perform this step twice.
OUTPUT PRESSURE TEST.This test is
performed in three stages. Apply hydraulic pressure of
1,500 psi to the PRESSURE port, and apply successive
plunger loads of 47 pounds, 124 pounds, and 190
pounds. As a result of these applications, the pressure
output readings at the BRAKE port should be 100 to 160
pounds on the first load, 660 to 750 pounds on the
second load, and 1,135 to 1,255 pounds on the third load.
LEAKAGE TEST.The leakage test for the power
section requires 1,500 psi of hydraulic pressure at the
PRESSURE port with the BRAKE and RETURN ports
open. With the valve shaft in the relaxed position, the
combined leakage from the open ports should not
exceed 25 cubic centimeters per minute for the last 4
minutes of a 5-minute period. If the unit checks out,
proceed to the next step.
With 1,500 psi still applied to the PRESSURE port,
plug the BRAKE port, and then extend the valve shaft
to midposition. Leakage from the RETURN port should
not exceed 25 cubic centimeters per minute for the last
4 minutes of a 5-minute period.
FLOW TEST.TO perform the flow test, you
should apply hydraulic pressure of 1,500 psi to the
PRESSURE port. Move the plunger between 3/8 and
5/8 of an inch. Minimum flow at the BRAKE port should
be 2 gpm, and there should be no evidence of chatter or
instability.
After testing is completed, remove the valve from
the test bench, flush it with hydraulic preservative oil,
drip-drain the unit, and plug all ports. The body should
be rubber-stamped with the cure date of the oldest
O-ring or packing and tagged with the date of the test
and the results.
MASTER BRAKE CYLINDER
Maintenance at the organizational level consists of
removal and replacement of the master brake cylinder.
Maintenance at the intermediate level consists of
disassembly, cleaning, inspection, repair and
replacement of seals and parts, lubrication, reassembly,
and testing.
Disassembly
Before disassembly, the Intermediate Repair"
section of the MIM or 03 manual should be used to make
sure that all parts, material, equipment, and facilities
required during repair are available.
WARNING
Before any removal, install an AN350-4 nut
on the threaded end of the piston rod to
bottom against the shaft bearing. This will
eliminate the possibility of injury to
personnel during disassembly because of
spring preload.
Disassemble the cylinder according to the proce-
dures provided in the Intermediate Repair section of
the MIM and/or 03 manual. Place spring-loaded
subassemblies in an arbor press or other device designed
to restrain parts while relieving the tension.
Cleaning
Wash all reusable parts of the Gladden master brake
cylinder with P-D-680 cleaning solvent. Use a bristle
brush to remove caked dirt from exterior surfaces. Use
a piece of soft, copper wire to remove obstructions from
ports and passages. Thoroughly dry all parts with a
clean, lint-free cloth or 20-psi compressed air.
Inspection
Conduct the inspection of parts under a strong light
and preferably with a means of magnification. Make the
following checks:
1. Check all parts for nicks, cracks, scratches, and
corrosion.
2. Check threaded parts for crossed or damaged
threads.
3. Check all packing grooves for surface defects
that might cut packings during installation or cause
failure during operation.
4. Check the bearing on the suspension rod at the
reservoir port end of the cylinder for freedom of rotation
and evidence of nut spots.
5. Check all springs for specified load at given
length. There should be no permanent set from test
loading, and springs should not wobble when they are
rolled across a hat surface.
Repair and Replacement
Polish minor nicks and scratches on metal parts with
crocus cloth (Federal Specification P-C-458C for steel
parts and P-C-451B for aluminum parts). During
polishing, make sure that all dimensions are maintained
within the specified limits and that seating and sealing
surfaces are not damaged.
12-48
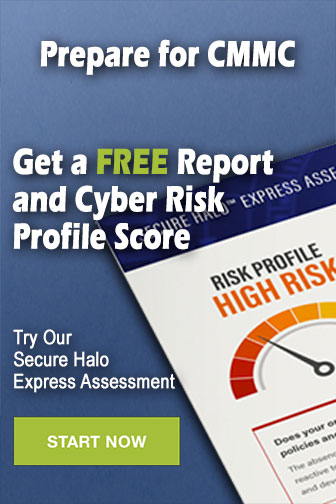