Tail rotor, 1-18
Tap testing, 14-23
Taper pins, 2-13
Teflon® hose, 5-2
Tempering, 15-39, 15-41
Tenisometer, 9-29
Tension, 1-20
Terminal swaging, 9-34
Terminals, 2-43
Test coil configurations, 15-12
Testing and operational checks, 3-18
Thermal relief valves, 7-24
Throatless shears, 13-12
Throwboards, 9-31
Tire construction, 11-10
Tire inflating, 11-23
Tire inspection, 11-16
Tire preventive maintenance, 11-26
dual installations, 11-28
nylon flat spotting, 11-28
uneven tread wear, 11-27
The rebuilding/retreading, 11-12
Tire retreading and repair, 11-26
nonserviceable tires, 11-26
serviceable tires, 11-26
Tire storage, 11-16
Titanium, 1-21
Titanium and titanium alloys, 1-32
Tool containers, 3-1
Tool control program, 3-1
quality assurance/analysis (QA/A) responsibil-
ities, 3-1
tool containers, 3-1
work center responsibilities, 3-2
Torches, 15-32
Torque, 10-2
Torquing computation, 3-22
Torquing of fasteners, 3-19
torquing computation, 3-22
torquing procedures, 3-19
Torquing procedures, 3-19
Torsion, 1-20
Touchup painting, 14-29
Touchup procedures, 14-32
acrylic nitrocellulose lacquer, 14-34
Du Pont Teflon® filled polyurethane paint, 14-34
elastomeric rain erosion-resistant coating
MIL-C-7439, 14-35
enamel finishes, 14-35
epoxy-polyamide MIL-C-22750, 14-34
epoxy-polyamide primer MIL-P-23377, 14-32
polyurethane paint systems, 14-33
zinc chromate primer TT-P-1757, 14-35
Translational lift, 10-4
Tread construction, 11-11
Tread patterns, 11-11
Trim tabs, 1-10
Trim system, 9-48
directional trim, 9-50
lateral trim, 9-48
longitudinal trim, 9-49
Trimetallic disc brakes, 12-61
Trouble analysis, 9-23
Troubleshooting aircraft systems, 3-15
Troubleshooting procedures, 3-17
Tube assemblies, 6-14
identification, 6-16
Tube bending, 6-9
Tube cutting, 6-8
Tube deburring, 6-9
Tube joint preparation, 6-11
flared fitting, 6-11
flareless fitting, 6-12
INDEX-19
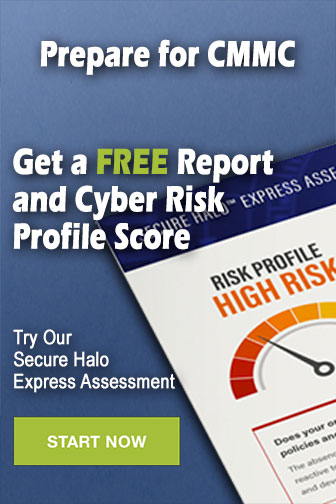