Figure 12-11.Shock strut operation.
also keep the nosewheel in a straight-ahead position
prior to landing when the strut is fully extended. Some
nose gear shock struts have the attachments for
installation of an external shimmy damper, which is
discussed later in this chapter.
Nose and main gear shock struts are usually
provided with jacking points and towing lugs. Jacks
should always be placed under the prescribed points.
When towing lugs are provided, the towing bar should
be attached only to these lugs.
All shock struts are provided with an instruction
plate that gives, in a condensed form, instructions
relative to the filling of the strut with fluid and inflation
of the strut. The instruction plate also specifies the
correct type of hydraulic fluid to use in the strut. The
plate is attached near the high-pressure air valve. It is of
the utmost importance that you always consult the
applicable aircraft MIMs and familiarize yourself with
the instructions on the plate prior to servicing a shock
strut with hydraulic fluid and nitrogen or air.
Figure 12-11 shows the inner construction of a
shock strut and the movement of the fluid during
compression and extension of the strut. The com-
pression stroke of the shock strut begins as the aircraft
hits the ground. The center of mass of the aircraft con-
tinues to move downward, compressing the strut and
sliding the inner cylinder into the outer cylinder. The
metering pin is forced through the orifice, and by its
variable shape, controls the rate of fluid flow at all points
of the compression stoke. In this manner, the greatest
possible amount of heat is dissipated through the walls
of the shock strut. At the end of the downward stroke,
the compressed air or nitrogen is further compressed,
limiting the compression stroke of the strut. If there is
an insufficient amount of fluid and/or air or nitrogen in
the strut, the compression stroke will not be limited, and
the strut will bottom out, resulting in severe shock and
possible damage to the aircraft.
The extension stroke occurs at the end of the
compression stroke, as the energy stored in the
compressed air or nitrogen causes the aircraft to start
moving upward in relation to the ground and wheels. At
this instant, the compressed air or nitrogen acts as a
spring to return the strut to normal. At this point, a
snubbing or dampening effect is produced by forcing the
fluid to return through the restrictions of the snubbing
device (recoil valve). If this extension were not snubbed,
the aircraft would rebound rapidly and tend to oscillate
up and down because of the action of the compressed
air. A sleeve, spacer, or bumper ring incorporated in the
strut limits the extension stroke.
MECHANICAL LINKAGE
The landing gear drag brace (fig. 12-12) consists of
an upper and lower brace that is hinged at the center to
12-10
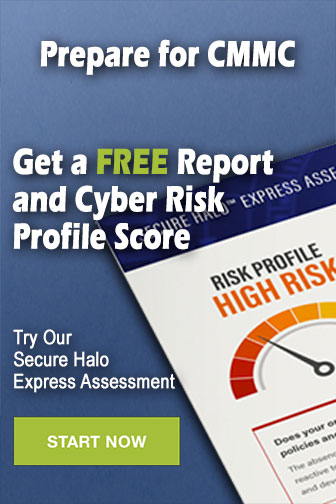