steering system is armed or activated automatically by
a switch actuated by the arresting hook when it is
extended. Both switches work in conjunction with a
weight-on-gear proximity switch (scissor switch)
located on one of the main landing gears. When the strut
is compressed a certain amount, the scissor switch
completes the electrical circuit to activate the nosewheel
steering. Nosewheel steering is desired for carrier
landing operations to prevent the nosewheel, or wheels,
from swiveling during rollback after arrestment.
Hydraulic Components
The main hydraulic components of the nosewheel
steering system are the nosewheel steering power unit
and selector valve. See figure 12-14.
NOSEWHEEL STEERING POWER UNIT.
The nose wheel steering power unit incorporates a
rotary, vane-type motor that is powered hydraulically
and is electrically controlled through various system
components to provide the nosewheel steering function.
When not in the steering mode of operation, the
nosewheel steering power unit serves as a nosewheel
shimmy damper.
The nosewheel steering power unit is mounted to
the nose landing gear cylinder, and the output drive gear
is meshed with the ring gear of the nose landing gear
torque collar. The torque collar deflects the nosewheel
as selected by rudder pedal positioning. Hydraulic fluid
displaced by the rotating vane during the steering mode
is directed back to the hydraulic return system.
When in the damping mode, fluid displaced by a
rotating vane is directed through an orifice restrictor
inside the nosewheel steering power unit to the opposite
side of the vane to provide the dampening feature.
NOSEWHEEL STEERING SOLENOID
SELECTOR VALVE.The nosewheel steering
solenoid selector valve is an electrically controlled and
hydraulically operated valve. The valve provides
pressure and return fluid porting during the steering
mode of operation.
Electrical Components
Nosewheel steering electrical components vary
greatly. The system uses three basic components. These
components are the feedback potentiometer, the
command potentiometer, and the steering amplifier.
FEEDBACK POTENTIOMETER.The feed-
back potentiometer is mounted to the nosewheel
steering power unit, and is mechanically linked or
geared to the vane motor shaft. See figure 12-14. During
the steering mode of operation, vane motor rotation
drives the feedback potentiometer. When driven, the
position transmitter provides a feedback signal to the
steering amplifier that is proportional to the amount of
vane motor rotation.
COMMAND POTENTIOMETER.The com-
mand potentiometer is attached to the rudder pedal
linkage. When the rudder pedals are moved, the
command potentiometer generates an electrical signal
proportional to the amount of rudder pedal deflection.
STEERING AMPLIFIER.The steering ampli-
fier sums the signals received from the feedback
potentiometer and the command potentiometer. This
summation is converted to a modulating signal that is
directed to the nosewheel steering power units servo
valve for nosewheel steering response. With the signals
from the command and feedback potentiometer
balanced, the servo is returned to a neutral condition,
and the nosewheel steering power unit stops at the
selected position.
ELECTRICALLY CONTROLLED NOSE
STEERING SYSTEM MAINTENANCE
Maintenance of an electrically controlled nose gear
steering system consists of operational checks, trouble-
shooting, system bleeding, and parts adjustment. These
maintenance functions normally require a joint effort on
the part of the AM and the AE personnel. See figure
12-15.
Operational Check
Perform an operational check to make sure the
quality of corrective or preventive maintenance is as
expected. Use the following procedures:
1. Jack the aircraft.
2. Connect electrical power and external hydrau-
lic power to the hydraulic system.
3. Manually turn the nose gear to about 30 degrees
to the right of center.
4. Operate the nose gear steering switch, and
check to see that nose gear steering does not engage.
5. Be sure that personnel and equipment are clear
of the arresting hook. Extend the arresting gear and
check to see that the nose gear returns to center.
12-14
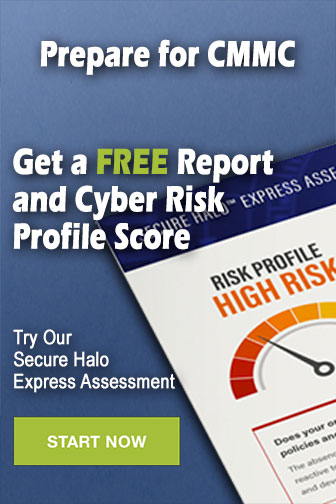