Accomplish the disassembly of the steering
dampener assembly in the order of the key index
numbers assigned to the exploded view illustration in
the Intermediate Repair Section of the MIM. Before
reassembly, clean all parts with a suitable solvent. Air
dry with warm, dry, low-pressure (10 psi) air. Nylon,
rubber, and Teflon® parts are replaced and not cleaned.
You should use the inspection standards in the MIM or
applicable 03 manual to inspect all parts of the steering
assembly.
Reassembly is essentially a reversal of the dis-
assembly order with appropriate quality assurance
checks at specific steps. Following complete re-
assembly, the steering assembly must undergo the
following bench tests:
1.
2.
3.
4.
5.
6.
7.
8.
9.
Proof pressure test
Input torque test
Steering resolution test (input motion versus
output motion)
Stall leakage test (output shaft in neutral and
input shaft fully engaged, and then measure
leakage
No steer test (steering assembly in neutral, and
then measure leakage at return)
External leakage test
Static friction torque test (clockwise and
counterclockwise torque required to start
movement of the output shaft in the power ON
and power OFF conditions)
Output torque test
Steady dampening rate test
The numerous steps involved in bench testing
components, such as the steering assembly and the
variations between it and other steering actuators, make
it impractical to cover the individual steps in detail. Shop
and quality assurance personnel must ensure that each
component repaired at the intermediate maintenance
level is actually in a ready-for-issue condition. This
requires vigilance on the part of all personnel. A
complete bench test must be made according to the test
arrangements provided in the MIM or the applicable 03
manual.
GENERAL LANDING GEAR
SYSTEMS MAINTENANCE
Learning Objective: Recognize procedures for
drop checks, troubleshooting, alignment and
adjustment, and the maintenance removal and
replacement of landing gear components.
Mandatory drop checks are required for all landing
gear maintenance procedures that involve the removal
and replacement of components, breaking of hydraulic
lines or fittings, and any adjustments to gear or door
linkages. Conditional maintenance requirements cards
call for a drop check whenever the aircraft experiences
a hard landing. In addition, regular drop checks are
required as part of the aircraft periodic inspection, even
if there has been no reported discrepancy.
DROP CHECK PROCEDURES
All drop check operations should be performed as
specified in the applicable maintenance instructions
manual (MIM). These procedures should be thorough
enough to ensure that the system is free of leaks and the
operational integrity of the system has been restored
following maintenance. Operational checks cover three
distinct areas. They are the operation of the landing gear
and doors, the operation of the landing gear position
indicator and warning system, and the operation of the
landing gear emergency system.
The first step in the drop check procedures is to
place the aircraft on jacks. Refer to chapter 3 of this
training manual.
Further preparation includes connection of a
hydraulic test stand and external electrical power,
removal of landing gear maintenance safety locks, and
the proper placement of the landing gear control handle.
As the operational procedure begins, check to make
sure that the landing gear doors do not close in the path
of the retracting main struts. This condition will be
obvious (with hydraulic and electrical power on the
aircraft) if the landing gear doors do not remain in the
full open position when the landing gear control handle
is placed in the UP position. Placing the landing gear
control handle momentarily to the UP and DOWN
positions several times will correct this condition by
removing air from the wheel door cylinders.
Regulate the hydraulic test stand to operate at a flow
of 4 gpm, and slowly increase hydraulic pressure. The
landing gear down lockpins should start to retract. They
should be fully retracted when the pressure reaches
12-18
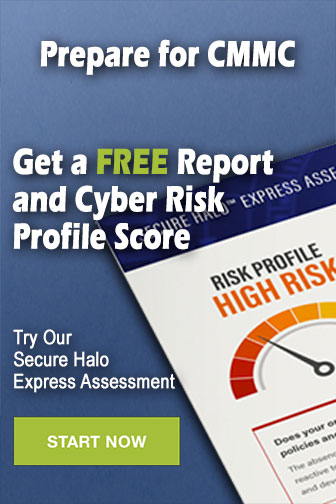