1,800 psi, and then all gear assemblies should start to
retract.
When the nose gear nears the up position, be sure
the fairing doors are cammed to the closed position, and
then check all gear doors to be sure they are closed and
locked when the position indicator indicates the
up-and-locked condition. Move the landing gear handle
down and check to see that the wheel fairing doors open
and gear assemblies extend. Visually check all gear
assemblies to ensure they are down and locked. With the
test stand regulated to 3 gpm at 3,000 psi, the gear should
make a complete cycle (up and down) in 12 to 14
seconds. The maximum pressure required to retract and
lock the gear is 1,800 psi at 4 gpm.
When you check the emergency extension of the
gear, first retract the gear normally, secure external
hydraulic pressure, place the landing gear handle in the
down position, and then pull and hold the emergency
extension handle fully aft. Visually check that all gear
assemblies are down and locked by observing the
landing gear position indicator in the cockpit, and then
release the emergency extension handle. It may be
neccssary to manually push the gear assemblies to the
down-and-locked position. The force required to push
the main gear to the locked position should not exceed
20 pounds applied to the axle hub. The force required to
push the nose gear to the locked position should not
exceed 10 pounds applied at the center line of the axle
hub. Make at least one complete normal cycle of the
landing gear, and then remove external power and
aircraft from jacks.
NOTE: Some aircraft require resetting of the
landing gear dump valves before recycling the
landing gear. Refer to the applicable MIMs.
TROUBLESHOOTING
Troubleshooting of the landing gear system, like all
hydraulic systems, requires that you understand the
theory of operation of the particular system and the
function and sequence of operation for each component.
Troubleshooting steps provided in the MIM are
normally aligned with the sequence of events or steps in
the operational checkouts. They provide an efficient
means of isolating the malfunction. The MIM requires
that each step in the operational checkouts be performed
in sequence. If trouble occurs during the procedure, it
must be corrected before proceeding with the next step.
These troubleshooting aids provide a logical cause for
many anticipated landing gear malfunctions, including
procedures for isolating and remedying the problem.
Refer to the system schematic for the particular system
and accompanying maintenance instructions, in
addition to sound reasoning, to pinpoint the cause for a
malfunction in an efficient manner.
Some landing gear malfunctions are related to
improper maintenance practices, with the lack of proper
lubrication being the predominant malpractice. A
review of past discrepancies and previous corrective
actions may also aid in analyzing malfunctions.
Occasionally, discrepancies that are reported as a
result of flight are difficult or even impossible to
duplicate on the deck. However, too many discrepancies
signed off with Could not duplicatesystem checks
4.0, or similar corrective actions, show up as repeat
malfunctions or as the cause of accidents. Every effort
should be made to locate a sound logical cause for a
reported malfunction by thoroughly checking the
system, each component, linkages, clearance, and
associated indicating systems. All phases of the
operational checkouts must be verified by a quality
assurance inspector.
Detecting internal leakage of components may
require the use of special equipment, such as the
ultrasonic leak detection translator or simple isolation
of components by disconnecting lines, applying
pressure, and measuring for allowable leakage limits.
If troubleshooting time is considered significant,
use a separate VIDS/MAF showing a common job
control number and Action Taken code Y. This form
provides input data that accounts for the troubleshooting
time separately from the actual repair time.
ALIGNMENT AND ADJUSTMENT
Improper rigging or adjustment of landing gear
linkages results in a significant number of unsafe or
hung landing gear discrepancies. Most landing gear,
when in an overcenter and locked position (up or down),
requires very little interference or binding to prevent its
initial movement.
Alignment of newly installed landing gear
assemblies or individual components should be in strict
accordance with the procedures outlined in the
applicable MIM. Complete assemblies are aligned in a
specified sequence, with designated steps throughout
the sequence that require quality assurance verification
before proceeding to the next step. Landing gear doors
may have to be deactivated or disconnected to check for
proper up lock actuation and gear up clearances.
12-19
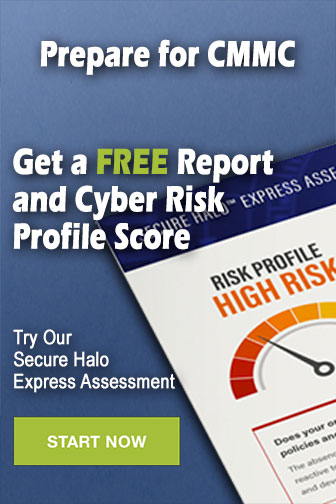