sheets should be stacked on the larger ones to avoid
unsupported overhead. Storage of transparent plastic
sheets presents no special fire hazard, as they are slow
burning.
Masking paper should be left on the plastic sheet as
long as possible. You should take care to avoid scratches
and gouges, which may be caused by sliding sheets
against one another or across rough or dirty tables.
Formed sections should be stored so that they are
amply supported and there is no tendency for them to
lose their shape. Vertical nesting should be avoided.
Protect formed parts from temperatures higher than
120°F. Protection from scratches may be provided by
applying a protective coating of masking paper or other
approved materials.
If masking paper adhesive deteriorates through long
or improper storage, making removal of paper difficult,
moisten the paper with aliphatic naphtha, which will
loosen the adhesive. Sheets so treated should be washed
immediately with clear water.
CAUTION
Aliphatic naphtha is highly volatile and
flammable. You should exercise extreme care
when using this solvent.
Do not use gasoline, alcohol, kerosene, xylene,
ketones, lacquer thinners, aromatic hydrocarbons,
ethers, glass cleaning compounds, or other unapproved
solvents on transparent acrylic plastics to remove
masking paper or other foreign material, as these will
soften and/or craze the plastic surface.
NOTE: Just as woods split and metals crack in
areas of high, localized stress, plastic materials
develop, under similar conditions, small
surfaces fissures called crazing. These tiny
cracks are approximately perpendicular to the
surface, very narrow in width, and usually not
over 0.01 inch in depth. These tiny fissures are
not only an optical defect, but also a mechanical
defect, inasmuch as there is a separation or
parting of the material. Once a part has been
crazed, neither the optical nor mechanical
defect can be removed permanently; therefore,
prevention of crazing is a necessity.
When it is necessary to remove masking paper from
the plastic sheet during fabrication, the surface should
be remasked as soon as possible. Either replace the
original paper on relatively flat parts or apply a
protective coating on curved parts.
REINFORCED PLASTICS
Glass fiber reinforced plastic and honeycomb are
used in the construction of radomes, wing tips, stabilizer
tips, antenna covers, fairings, access covers, etc. It has
excellent dielectric characteristics, making it ideal for
use in radomes. Its high strength/weight ratio, resistance
to mildew and rot, and ease of fabrication make it
equally suited for other parts of the aircraft.
The manufacture of reinforced plastic laminates
involves the usc of liquid resins reinforced with a filler
material. The resin, when properly treated with certain
agents known as catalysts, or hardeners, changes to an
infusible solid.
The reinforcement materials are impregnated with
the resin while the latter is still in the liquid (uncured)
state. Layers or plies of cloth are stacked up and heated
under pressure in a mold to produce the finished, cured
shape. Another technique, culled filament winding,
consists of winding a continuous glass filament or tape,
impregnated with uncured resin, over a rotating male
form. Cure is accomplished in a manner similar to the
woven cloth reinforced laminates.
Glass fiber reinforced honeycomb consists of a
relatively thick, central layer called the core and two
outer laminates called facings. (See figure 1-22.)
The core material commonly used in radome
construction consists of a honeycomb structure made of
glass cloth impregnated either with a polyester or epoxy
or a combination of nylon and phenolic resin. The
material is normally fabricated in blocks that are later
cut on a band saw to slices of the exact thickness desired,
or it may be originally fabricated to the proper thickness.
The facings are made up of several layers of glass
cloth, impregnated and bonded together with resin. Each
layer of cloth is placed in position and impregnated with
resin before another layer is added. Thicker cloths are
normally used for the body of the facings, with one or
more layers of liner weave cloth on the surface.
The resins are thick, syrupy liquids of the so-called
contact-pressure type (requiring little or no pressure
during cure), sometimes referred to as contact resins.
They are usually thermosetting polyester or epoxy
resins. Cure can be affected by adding a catalyst and
heating, or they can be cured at different temperatures
by adjusting the amount and type of catalysts. Inspection
1-43
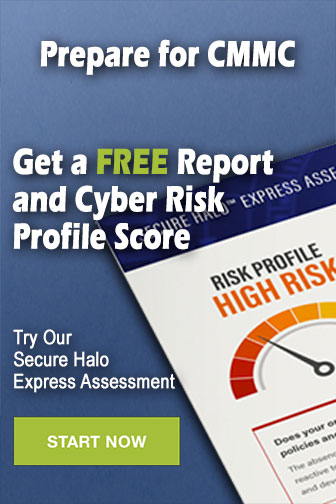