supports. Flexible grommets or hose should be used
at points where the tubing passes through bulk-
heads.
REPAIR
Tube repair is divided into two categories
temporary and permanent. Temporary repairs are
made with splice sections fabricated with flared ends
or preset MS sleeves. The splice sections are to be
replaced by a permanent repair or new tubing
assembly at the next rework cycle. Temporary or
emergency repairs should be limited to cases that are
due to unavailability of equipment, material, or
unusual circumstances.
Cut and remove the damaged section of tubing.
Remove the rough edges of the remaining tube ends.
Clean the tubing ends with a lint-free wiping cloth.
Position the AN818 nuts and AN819 sleeves on the
tubing ends (fig. 6-23). Flare the tubing. Install
AN815 unions. Position the AN818 nuts and AN819
sleeves on the new section. A new section is not
required when the length of the union is longer than
the damaged section. Install the new section of tubing
and tighten the AN818 nuts. Permanent repairs
include removal of minor damage on tubing and
fittings and the replacement of line sections or fittings
by Permaswage or Dynatube swaging equipment, or
by induction brazing.
NOTE: Induction brazing is limited to
depot-level repair. Tube assemblies used for
engine-related hydraulic, fuel, oil, vent or
drain lines usually have brazed or welded end
fittings.
These engine-related tube
assemblies are normally fabricated from
corrosion-resistant steel.
Some minor surface damages to tubing are
acceptable, as described in inspection of tubing
damage. A nick that is not deeper than 15 percent
of the wall thickness of aluminum, aluminum
alloy, or corrosion-resistant steel is acceptable
after being reworked by burnishing with hand
tools. Minor damage to fittings is defined as
Figure 6-23.Temporary tubing repair.
6-23
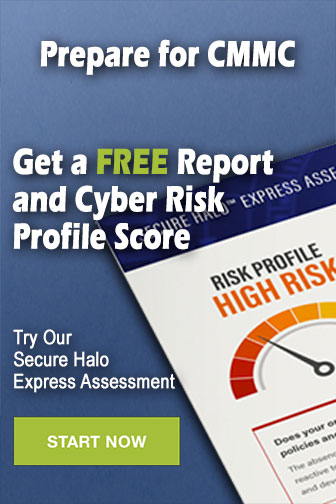