on the pressure plate by the pistons. This small
movement of the adjusting pins and tubes, relative to the
grips, is equivalent to the combined wear of all the discs.
When pressure is removed from the brake, the return
springs return the pressure plate and the brake pistons
to the designed reset clearance and maintain a constant
displacement.
Maintenance
Intermediate maintenance of the trimetallic brake
assembly consists of disassembly, cleaning and inspec-
tion, wear pad replacement as necessary, reassembly,
and testing. A brief description of each follows.
DISASSEMBLY.Place the brake assembly with
the brake housing down and remove the brake housing
bolts. Remove the backing plate and all discs from the
torque tube, and then remove the torque tube. Turn the
brake over and remove the self-locking nuts to release
the return pins. Remove the tube and grip assemblies,
pressure plate, and the remaining return spring parts.
The tube and grip assemblies should not be
disassembled. If they require replacement, replace the
complete assembly as a unit.
The piston insulator is removed from the pistons,
and the pistons are removed from the brake housing by
threading a return pin into the threaded hole in the piston
and pulling slowly. Exercise care to avoid damage to the
seal groove and cylinder walls. Remove the bleed valve
assembly and the brake inlet plug assembly.
CLEANING AND INSPECTION.Dust and
loose grit are removed by using low-pressure air, and
then all parts are cleaned in a P-D-680 cleaning solvent
and dried with a clean, lint-free cloth.
All metal parts are visually inspected for cracks,
wear, or other damage, as specified in the Intermediate
Repair section of the MIM. Some parts may require
inspection by one of the nondestructive methods. The
return spring is inspected for proper resilience. The
amount of force required to move the grips on each tube
and grip assembly is checked with a special tube and
grip tester.
The rotating disc is inspected for cracks, distortion,
and thickness. The disc must be replaced if it is worn
below 0.2-inch thickness, if it is cracked, or if the
friction mix is worn unevenly. The friction mix maybe
pitted up to 0.5 square inch in any segment.
The stationary disc is inspected for cracks and
thickness. If the minimum thickness is less than 0.3 inch
or the disc is cracked, it should be replaced.
The backplate and pressure plate should be replaced
if they are cracked. If the wear pads are worn to less than
0.088-inch tltickness, they should be replaced.
WEAR PAD REPLACEMENT.Wear pad re-
placement on the pressure plate and the backing plate is
authorized. Drill out rivets that hold the worn pads.
Discard the worn pads. Check the plates for cracks,
deformation, and rivet hole elongation. Use a standard
squeeze rivet machine to rivet the replacement wear
pads to the plates, using the type of rivet specified in the
applicable MIM. The rivet bucktail must be below the
surface of the wear pad, Rivets with more than one crack
visible in the bucktail or with less than 50 percent of the
circumference of the formed head flush with the sides
of the countersunk area are not acceptable. The new
wear pads must be surface ground to 0. 100-inch
thickness, and should be flat within 0.010 inch after
grinding. The reworked plates should be vapor
degreased to remove all oil and grinding material. The
dried plates should be wrapped in clean, heavy paper for
protection until they are replaced in the brake assembly.
REASSEMBLY.Reassembly of the trimetallic
brake is essentially in the reverse order of disassembly.
Lubricate the packings, retainers, cylinder walls, and
other contacting surfaces within the brake housing with
a light coating of MIL-G-8 1322, general-purpose
aircraft grease before reassembly. Apply MIL-G-6032B
grease to the piston side of the piston insulators.
Lubricate the brake housing bolts and the contacting
surfaces of the bolt heads with antiseize compound. The
coating of these bolts and the contacting surface of the
bolt heads, followed by torquing, are referred to in some
MIMs as Lubtork.
TESTING.The reassembled trimetallic brake
must be tested to ensure the quality of maintenance.
Connect the brake assembly to a hydraulic test stand and
apply 25 psi to the inlet port. Open the bleeder valve
until air-free fluid flows from the valve. Increase the
pressure to 1,000 psi for 2 minutes and check for leaks.
Relieve and reapply 1,000 psi several times, and then
release the pressure slowly to 90 psi. Holding the 90-psi
pressure, measure the clearance between the pressure
plate and the first rotating disc. Minimum clearance
must be 0.065 inch. If used discs were reinstalled, check
for proper rotation. Secure the test stand, disconnect the
brake, and plug the inlet port to prevent contamination.
12-62
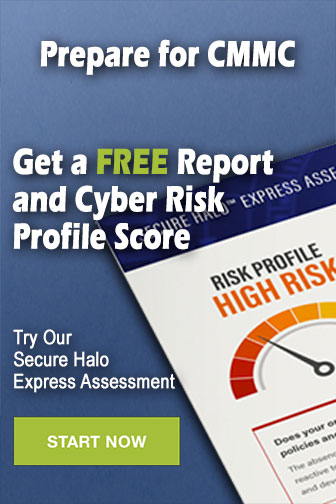