1.
2.
3.
4.
5.
Control orifice No. 2 (release)
6. Pressure
11. Return seat
Control spring
7. Brake
12. Release piston
Return
8. Poppet
13. Control piston
Second step solenoid pilot valve
9. Ball check
14. Control orifice No. 1
Filter
10. First step solenoid pilot valve
Figure 12-55.Antiskid control valve schematic.
SKID CONTROL SYSTEM
MAINTENANCE
Learning Objective: Recognize the organi-
zational- and intermediate-level maintenance
requirements for the proper operation of the
skid control system.
An antiskid test set is available for personnel in the
AE rating to use on the antiskid system. The operational
test normally requires a joint effort on the part of both
AM and AE personnel.
Organizational maintenance on the antiskid control
valve, shown in figure 12-55, is limited to removal and
replacement. Intermediate level repair of the valve
consists of cure-date seal and parts replacement in
accordance with the procedures provided in the
Intermediate Maintenance section of the MIM.
Following repair, the valve must be tested to verify
proper operation both hydraulically and electrically.
Trouble analysis/troubleshooting of the antiskid
system is generally accomplished by personnel of the
AE rating. The steps provided for using the antiskid test
set will pinpoint the causes for most malfunctions.
Those steps that do not meet the specified results are
investigated, parts are replaced as necessary, and the
complete operational check is repeated to verify that the
malfunction has been corrected.
HYDRAULIC UTILITY SYSTEMS
MAINTENANCE
Learning Objective: Recognize the different
hydraulic utility systems and their maintenance
procedures.
12-63
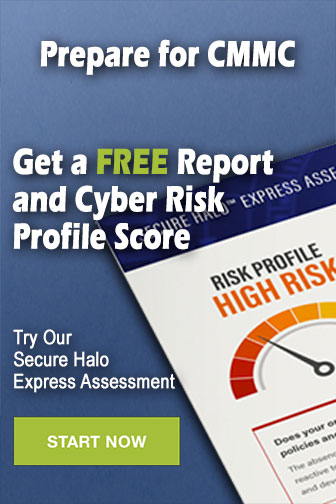