Figure 12-59.Centering spring.
2. Adjust the rod ends of both centering springs to
reach the attaching pivot holes. Threads must be visible
through the rod end inspection hole. See figure 12-59.
3. Tighten the nuts on the attaching bolts finger
tight. Safety with cotter pins.
4. Torque the rod end jam nuts to 270-300 inch-
pounds and safety with Iockwire, as shown in figure
12-59.
5. Check lateral movement of the hook in
accordance with the procedures prescribed in the MIM.
Intermediate-level maintenance of the centering
springs consists of checking the disassembled parts for
scoring, corrosion, nicks, structural deformation, or
failure. Nonferrous parts are subjected to fluorescent
penetrant inspection and ferrous parts to magnetic
particle inspection. The diameter of all parts and the free
length dimensions of the two springs, shown in figure
12-59, are checked against the values given in the parts
tolerance tables provided in the MIM.
WARNING
Disassembly and assembly require extreme
caution. The spring force is in excess of 500
pounds. Failure to observe the proper safety
precautions could result in personnel injury.
Post repair testing includes checking the breakout
force required to extend and compress the springs. Force
required is 560 60 pounds. The spring should extend
1.60 inches 0.03 inch and compress 1.40 inches 0.03
inch from neutral.
CATAPULT LAUNCH SYSTEM
The purpose of the nose landing gear catapult
launch system is to provide a means of directing the
aircraft into position for catapult launching, as well as
being connected automatically to the ships catapult
equipment. Such a device eliminates the necessity for
flight deck personnel to manually connect catapult
12-68
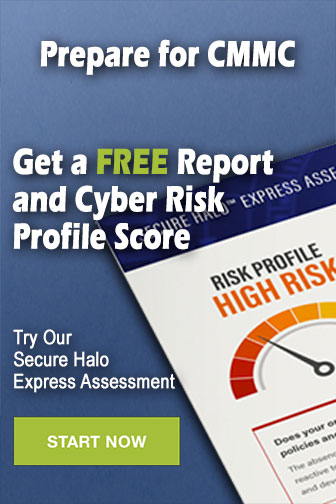