With the engines operating or external electrical and
hydraulic power applied, the probe is extended by
placing the refueling probe switch in the EXTEND
position. This electrically actuates the solenoid selector
valve to supply restricted hydraulic flow to the extend
port of the probe-actuating cylinder. The restrictor
valves control the rate of cylinder extension and
retraction. The check valve prevents pressure surges in
the hydraulic return system from unlocking the
probe-actuating cylinder during flight.
After disengaging the probe nozzle from the tanker
drogue, hold the air refueling switch in RETRACT to
actuate the solenoid selector valve to supply pressure to
the retract port of the probe actuating cylinder, causing
it to retract and lock the probe into place. A cockpit
advisory panel transit light goes out whenever the probe
is locked in the extended or retracted position. A probe
floodlight, which illuminates the probe tip for visual
contact with the refueling drogue at night, is on
whenever the refueling probe switch is in EXTEND and
exterior lights are on. The floodlight goes out when the
refueling probe switch is placed in RETRACT or OFF.
Organizational maintenance of the air refueling probe
system normally consists of operational checks,
troubleshooting, rigging and adjusting, and removal and
installation of components.
To perform an operational check of the air refueling
probe system, the hydraulic system must be pressurized
to 3,000 psi, external electrical power applied, and the
in-flight refueling circuit breaker engaged. Before
actuating the system, ensure that all personnel and
equipment are clear of the area of probe travel. The
extension cycle rotates the probe from its stored locked
position to an extend locked position.
Position the fuel probe switch to EXTEND. Check
for proper probe extension and probe locking. If
operation of the probe is not smooth, check for air in the
system. Position the fuel probe switch to RETRACT and
check for proper probe retraction. The complete
extension cycle should be from 5 to 7 seconds, with the
retraction cycle taking from 9 to 11 seconds.
Troubleshooting of the system should include a
thorough knowledge of the malfunction compared to
proper system operation and referral to system
schematics and troubleshooting tables provided in the
MIM. System rigging, component removal and
installation, and all other maintenance should be in
accordance with the procedures and safety precautions
outlined in the MIM.
Intermediate maintenance of faulty components
consists of cure-date kit installation and testing in
accordance with the Intermediate Maintenance
section of the MIM or the applicable (03) overhaul
manual.
WING FOLD SYSTEMS
There are miscellaneous differences in the design
and operating characteristics of the various
hydraulically operated systems, and the wing fold
systems are no exception. Basically similar components
perform similar functions with only minor variation in
part nomenclature and physical design.
The wing fold system described in the following
paragraphs will point out some of these differences.
Refer to the wing fold system schematic shown in figure
12-63 as you read the following paragraphs.
The wings arc unlocked by lifting the wing fold
handle up and forward until it reaches the first stop. This
action operates the cable and pushrod mechanisms that
control mechanical locking of the wing lock cylinders.
This same action, through the pushrod connected to the
mechanical locks, causes the warning flags to appear on
top of the wings. Further movement of the wing fold
handle at this point is prevented by a spring-loaded
mechanical latch that blocks the crank at the wing lock
cylinder.
With flight controls in the proper position and
weight on the wheels, the wing fold lockpin switch is
placed at UNLOCK. Power is supplied to the unlock
side of the wing lock selector valve, allowing combined
system utility hydraulic pressure to the four wing lock
cylinders in each wing. Pressure in the wing lock
cylinders moves the lock shaft to retract the wing
lockpins. After completion of this action, the wing fold
control handle can be moved to the full forward position,
operating the wing fold selector valve in each wing and
porting hydraulic pressure through flow regulators to
the wing fold actuating cylinders, which extend and
cause the wing to fold.
The wings are spread by moving the wing fold
control handle aft to the first stop, mechanically
positioning the wing fold selector valve in each wing to
port hydraulic pressure through flow regulators to the
wing fold cylinders, causing them to retract and spread
the wings. The wing fold control handle is held at the
first stop by the retracted lockpins,
rotation of the lock shafts and cranks.
which prevent
12-71
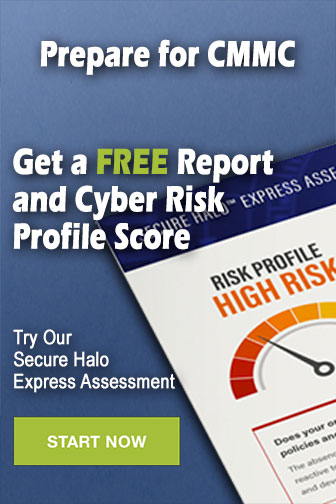