exchanger and a condenser/vent suit heat
exchanger and water extractor, which removes 90
percent of the moisture content through repeated
heating and cooling. The conditioned dry air is
transported to the turbine end of the refrigeration
turbine/compressor assembly where it is cooled
by rapid expansion. Both the turbine and
compressor are protected from overheat damage
by the turbine and compressor protective temper-
ature sensors. As the cold dry air leaves the
turbine, it is mixed with warm air from the
environmental control and related systems, and
then it is routed to cockpit and avionics
compartments to satisfy environmental control
requirements. Air cycle ACS components are
discussed in the following paragraphs.
Primary Heat Exchanger
The primary heat exchanger (fig. 3-2) is a
cross-flow, air-to-air heat exchanger that uses ram
air to initially cool hot engine bleed air. It operates
on the same principle as the radiator in an
automobile with the bleed air replacing the liquid.
Hot bleed air is transported through the heat
exchanger core where ram air, forced across the
core by aircraft forward motion, absorbs the heat
from the bleed air, reducing the air temperature.
During ground and low-speed operation, cooling
air is pulled across the heat exchanger core by
ejecting hot air into the heat exchanger exit duct.
The ejected air is controlled by the primary
ejector valve in response to signals from the Air
Data Computer (ADC). The cooled air exiting the
heat exchanger is divided into two ducts that
provide air at varying temperatures for use in
related systems. The temperature difference
occurs because of the distance the bleed air travels
through the heat exchanger core.
Primary Ejector Valve
The primary ejector valve is a normally open,
in-line poppet, pneumatically actuated, solenoid-
controlled shutoff valve. The valve controls the
flow of bleed air to the primary heat exchanger
ejector in the primary heat exchanger exit duct.
The hot bleed air flowing through the ejector
nozzles causes an area of low pressure to form
at that point. This causes ambient air to flow
across the core of the heat exchanger from the
high pressure side to the area of low pressure. The
valve is controlled by an electrical signal from the
ADC. At airspeeds below 100 knots, the ADC
provides an electrical ground that energizes the
primary ejector control relay to remove power
from the valve solenoid, allowing differential
pressure to hold the valve open. At airspeeds
above 100 knots, the ADC ground is lost. This
de-energizes the primary ejector control relay to
apply power to the valve solenoid, allowing spring
tension to close the valve.
Flow Modulating System
Pressure Regulator Valve
The flow modulating system pressure regula-
tor valve is a combination butterfly, modulating
valve, and solenoid shutoff valve. The modulating
valve is normally open and pneumatically
actuated. The valve is in the distribution ducting
between the primary heat exchanger and the
refrigeration turbine/compressor assembly. The
valve uses electrical signals from the avionics
temperature/flow sensor by way of the ACS
temperature/flow controller to modulate down-
stream pressure. The valve is also connected
pneumatically to the turbine and compressor
protective temperature sensors, which override all
other valve functions to close the valve to
protect the refrigeration turbine/compressor
assembly from heat damage during overtemper-
ature conditions. The solenoid shutoff is con-
trolled by the environmental control system (ECS)
mode switch, which allows the valve to be opened
or closed by dumping control air from the butter-
fly diaphragm chamber. The valve also includes
a visual position indicator. The indicator is built
into the valve housing and shows the position of
the butterfly.
Avionics Ram Air Servo
The avionics ram air servo monitors the
differential pressure of bleed air upstream and
downstream of the flow modulating system
pressure regulator valve. If the upstream-pressure
is less than 35 psi and the differential pressure is
less than 10 psi, the avionics ram air servo drives
the avionics ram air valve open. If downstream
pressure is less than 4 psi, the avionics ram air
servo drives the avionics ram air valve open. The
operation of this valve, though not a part of the
ACS, ensures that avionics will receive sufficient
cooling air in the event of a low or no airflow
condition from the ACS.
3-5
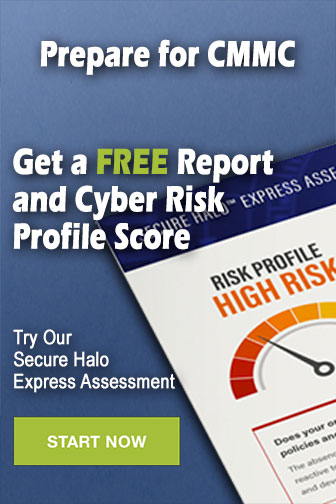