the annular section between the duct wall and re-
entrant discharge duct. Approximately 3 percent
of the total airflow is also shaved off as scavenge
air. The scavenge air/water enters the outer
chamber, which is surrounded by a perforated
muff. In this chamber the water droplets are
separated from the scavenge air. The dry scavenge
air flows into an end chamber, through a baffle
and out through the scavenge port. The water
flows through the perforations into a sump and
out through the drain port to the water spray noz-
zle where it is used to augment ram air cooling
in the secondary heat exchanger.
Refrigeration Turbine/
Compressor Assembly
The refrigeration turbine/compressor assem-
bly is a centrifugal compressor with a turbine
wheel mounted at each end of a common shaft.
The compressor end receives partially conditioned
air from the flow modulating system pressure reg-
ulator valve, where it is compressed to approx-
imately double its inlet value. The air is
transported through the secondary heat ex-
changer, reheater heat exchanger, condenser/vent
suit heat exchanger, and water extractor before
entering the turbine end of the refrigeration
turbine/compressor assembly. The conditioned,
dry air flows through turbine nozzles to the
turbine wheel where heat energy is changed to
mechanical energy, driving the compressor. The
expanded, cold air exhausting from the turbine
is transported back through the reheater heat
exchanger, into ducting, where it is used for
environmental control.
Anti-Ice Add Heat Valve
The anti-ice add heat valves is a normally
closed, electrically controlled, pneumatically
actuated, modulating valve. The valve is between
the windshield anti-ice/rain removal manifold and
the turbine outlet. The valve is controlled by
electrical signals from the ACS temperature/flow
controller and differential pressure sensed across
the condenser/suit vent heat exchanger. This valve
maintains the turbine outlet temperature as
required to prevent icing by adding hot air to the
conditioned, cold air.
SYSTEM TESTING
Air-conditioning test sets (testers) are used
to test ACSs for proper operation and to
troubleshoot system malfunctions. Some newer
aircraft being introduced into the fleet have an
aircraft installed tester. This built-in tester (BIT)
performs many tests of the system in flight. The
following is an example of the F-18 automatic test
sequence.
The ACS BIT starts when electric power is
applied to the ACS temperature/flow controller.
In-flight BIT is a complete sequence of tests on
the ACS temperature/flow controller and 10
electrically interfacing components. Nine seconds
are required for a complete BIT sequence, and
the BIT sequence is repeated every 90 seconds.
If the same test indicates a failure on two
consecutive BIT sequences, the BIT processor
removes a ground from the signal data converter,
and a maintenance code is recorded. After a
maintenance code is recorded, BIT is inhibited
until electrical power is removed and reapplied.
When the aircraft is on the ground, BIT operation
is the same as in-flight BIT except that only part
of the BIT sequence is performed.
BIT tests the flow modulating system pressure
regulator valve to produce the following
indications:
BIT tests for OPEN CIRCUITS in the valve
torque motor and position feedback transducer
during any mode of operation, and will produce
a failure signal if an open circuit is detected.
BIT tests for VALVE STUCK OPEN condi-
tion by comparing a high avionics airflow
condition with a high torque motor current
(closing signal to valve). When both of
these indications exist, a failure signal is
produced.
BIT tests for VALVE STUCK CLOSED
when airflow to the cabin and avionics are low.
The BIT failure signal is inhibited if the valve
position transducer indicates the valve is full
open.
COMMON AIR-CONDITIONING
COMPONENTS
Some components and hardware are com-
mon to all ACSs. Bleed-air ducting is manu-
factured from stainless steel and can withstand
pressures up to 450 psi and temperatures up to
800°F (425°C). These ducts are covered with
3-7
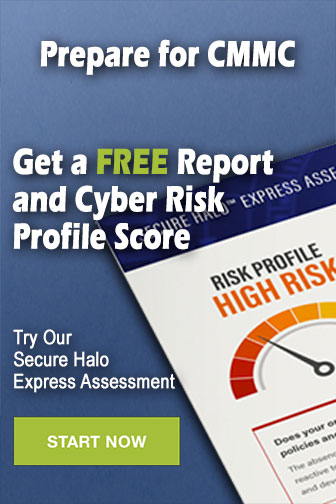