pressures in excess of 3,750 psi. The gas then flows
through the priority valve (PRIV). This valve is
set to stop the flow of gas from the supply
cylinders when cylinder pressure falls below
200 ± 10 psi. From the priority valve, gas flows
to the pressure regulating valve (PRV). Pressure
indicated on the high-pressure gauge (PG-1) is
reduced to 50±5 psi by the pressure regulating
valve. The reduced pressure is shown on the low-
pressure gauge (PG-2). Gas then flows to the relief
valve (RV-2), which is preset to 75+ 0, 10 psi.
From the relief valve, gas passes through the
heater assembly (HIR), where the gas is heated
to 285°F. The heated gas flow is then directed
through the flow control orifice (ORF), which
maintains the flow of gas at 0.20±0.017 pounds
per minute at the regulated pressure of 50 ± 5 psi.
The gas that exists in the filler valve (FLRV) will
be at a temperature of 225±25°F.
Electrical power for the heating element in the
heater (HTR) is controlled by the pressure switch
(PSW) and two temperature switches. When gas
pressure of 50±5 psi is reached, the pressure
switch energizes the temperature control circuit
and allows the heater assembly to warm. The
temperature switch breaks contact within the
circuit when the heater assembly temperature
exceeds 285°F, and re-establishes contact when
the heater assembly cools to 270°F, thus main-
taining a temperature of 250°F to 260°F at the
heater- assembly discharge.
The high temperature switch functions as a
safety switch. This switch is set to break the heater
circuit when heater assembly temperature exceeds
300°F, and re-establish the circuit when
temperatures fall below 273°F. For operational
use of the purging unit, seethe users manual sup-
plied with the unit or the Liquid Oxygen, System
Gas Purging Set, NAVAIR 19-25D-27.
GASEOUS OXYGEN
SERVICING TRAILERS
Learning Objective: Identify components
and operating procedures for gaseous
oxygen servicing trailers.
There are several different models of gaseous
oxygen servicing trailers currently in use by naval
activities. They are all similar in operation;
therefore, only one, the type NO-2, manufactured
by Aeroil Products, Incorporated, is described
here. The trailer is shown in figure 5-13.
Equipment provided on the trailer includes six
manifold control valves with pressure gauges; an
upper and lower manifold; two pressure
regulators; a recharge valve; four shutoff valves;
a drier assembly, six cylinders, and connecting
flexible hoses; and a servicing hose fitted with a
line servicing valve fitted with a high-pressure
charging adapter. The function of each of these
components is described in the following text.
COMPONENTS
Complete familiarity with the following trailer
components is a basic prerequisite for safe
operation.
MANIFOLD CONTROL VALVES. The six
manifold control valves serve to shutoff the flow
of oxygen from the cylinders to the system being
charged. These valves are lever-type valves. The
manifold control valves should not be used for
long-time storage. Always use the handwheel type
valves located on the cylinders.
UPPER MANIFOLD. The upper manifold
provides connections/mounting for the six
manifold control valves with pressure gauges (each
connected to a supply cylinder), a recharge valve,
and two upper/inlet shutoff valves that connect
to the inlet side of the regulators.
PRESSURE REGULATORS. The pressure
regulator controls the charging pressure when the
trailer is being used to service aircraft oxygen
systems. Only one pressure regulator is used
during operation. The spare is provided to ensure
uninterrupted operation should one fail.
RECHARGE VALVE. The recharge valve is
provided as a means of recharging the trailer
cylinders directly through the upper manifold
without the necessity of removing the cylinders.
When not in use, the valve adapter should be
fitted with a dust cap.
SHUTOFF VALVES. There are four shutoff
valves, one on the inlet side of each pressure
regulator and one on the outlet side of each
regulator. These shutoff valves control the flow
of oxygen from the upper manifold to the lower
manifold, via the regulator.
When the shutoff valves on the inlet and outlet
sides of the regulator are open, the pressure
regulator is ready for use. By turning the regulator
control-handle clockwise, the pressure (as read on
5-16
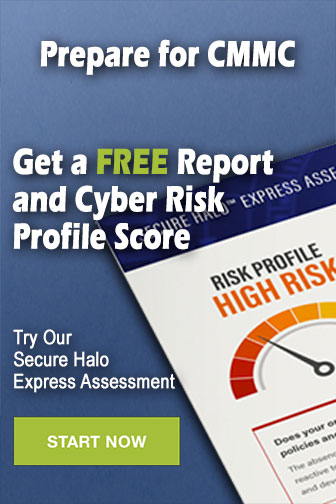