heat valve to maintain the selected temper-
ature.
MANUAL TEMPERATURE CONTROL
Manual temperature control is selected by
setting the ECS mode switch to MAN. In the
manual mode, adjusting the cabin knob of the
suit/cabin temp control determines the control
signal sent to the cabin add heat valve.
EQUIPMENT COOLING SYSTEMS
Learning Objective: Recognize the source
for avionics cooling air; identify com-
ponents of avionics cooling systems and the
function of each component.
As electronics and avionics in naval aircraft
became more common and more sophisticated,
it was discovered that the heat generated by this
equipment was becoming excessive for proper
operation. A means of keeping the avionics at a
proper operating temperature was needed. To
overcome this problem, some aircraft have.
separate ACS for equipment cooling, while
others use conditioned air diverted from the
environmental ACS.
If the equipment ACS is an air-to-air type, its
operation is the same as the environmental ACS
discussed at the beginning of this chapter. Only
operating temperatures will be different. The
other type of equipment air conditioning (vapor
cycle) operates on the same principal as a home
ACS and will be discussed later in this chapter.
AIR-TO-AIR SYSTEM
The F-18 aircraft avionics cooling system (fig.
3-11, a foldout at the end of this chapter)
controls and transports conditioned air to the
various avionics packages and equipment bays.
Conditioned air from the air cycle ACS is
transported to the avionics flow valve where
inlet pressure and airflow is controlled in response
to signals from the avionics flow/temperature
sensor through the ACS temperature/flow
controller. Airflow rates are matched to the
individual cooling requirements of each equip-
ment package or bay.
Ground cooling of the avionics equipment
bays is provided by an avionics ground cooling
fan. The cockpits avionics equipment cooling is
done by four cockpit avionics cooling fans, two
in the forward cockpit and two in the rear cockpit.
Emergency ram air cooling for essential
avionics equipment is provided by an emergency
ram air scoop and avionics ram air valve.
The avionics cooling components are discussed
in the following paragraphs.
Avionics Airflow Valve
The avionics airflow valve is a normally open,
pneumatically actuated and controlled pressure
regulating valve. The valve is in the avionics
supply line and maintains a pressure differential
of 1.5 psi between an externally sensed upstream
duct pressure and an externally sensed cabin duct
pressure. Actuator spring pressure holds the valve
butterfly to full open. Cabin pressure is sensed
on one side of the control diaphragm and
upstream valve pressure is sensed on the other
side. If no pressure is applied to the control
diaphragm, the feedback spring holds the control
nozzle closed. Any external supply pressure
applied under this condition overrides the actuator
spring pressure and closes the valve.
Avionics Flow/Temperature Sensor
The avionics flow/temperature sensor is made
up of a flow sensor and temperature sensor
enclosed in a single unit. The sensor is in the
supply line downstream of the avionics airflow
valve. The sensor provides signals to the flow
sensing and anti-ice temperature sensing bridges
in the ACS temperature/flow controller for
automatic operation of the flow modulating
system pressure regulator valve and anti-ice add
heat valve.
Avionics Ram Air Valve
The avionics ram air valve is a normally open,
pneumatically closed, remote-controlled shutoff
valve. It is between the secondary heat exchanger
ram air inlet and the avionics supply line. The
valve provides ram air augmentation for avionics
cooling if cooling airflow drops below an
established limit. The valve is closed by
3-15
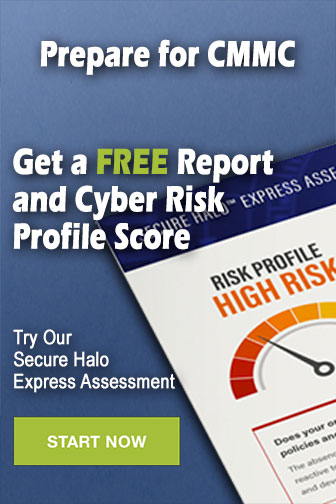