cooled and the transfer of this heat to the primary
coolant through the evaporator assembly.
A header assembly attached to the discharge
side of the evaporator assembly directs the
secondary coolant air to distribution ducts
throughout the electronic equipment compart-
ment. A filter between the header assembly and
the evaporator assembly removes dirt and dust
particles and traps moisture from the air.
The closed system consists of the evaporator
group assembly and the condenser group
assembly. The coolant circulates between the
evaporator group assembly (where it absorbs heat)
and the condenser group assembly where it
discharges or dissipates the heat to the atmosphere
through the vapor cycle scoop.
During flight, ram air flowing through the
scoop cools the condenser group assembly. The
airflow through the scoop is controlled by a
condenser pressure control system. The actuator
in the scoop modulates the airflow through the
scoop to provide sufficient cooling for con-
densation of the refrigerant.
When the aircraft is on the ground with
engines running and ram airflow is insufficient
for cooling, a condenser ejector air shutoff valve
opens to permit engine bleed air to discharge
through the ejector assembly. The ejector consists
of a set of tubes that permit bleed air to escape
into the ram air duct behind the condenser. The
escaping bleed air creates a negative pressure
(suction) area behind the condenser and causes
ambient air to be drawn into the scoop and across
the condenser.
If the heat load applied to the evaporator and
the ram air temperature and flow were constant,
a simple opening would be all that was required
to control the boiling point of the refrigerant
entering the evaporator. Since these three factors
are not constant, they must be compensated for.
In the model VEA6-1 system, if the heat load is
changed, the flow of refrigerant is changed by
using a thermostatic expansion valve in place of
a fixed opening. The pressure of the refrigerant
in the evaporator is maintained constant,
regardless of the refrigerant flow, by varying the
speed of the compressor.
When the EQUIPMENT COOLING switch
is set to ON, solenoid-operated shutoff valves are
energized and hydraulic pressure is directed to the
evaporator fan motor and the compressor motor.
The compressor motor will be automatically shut
off when either aircraft engine is in autofeather
and the landing gear is down. The evaporator fan
motor will continue to operate.
With the evaporator fan and compressor
motors operating, low-pressure, low-temperature
refrigerant Freon 12 vapor enters the compressor
assembly through the low-pressure line leading
from the evaporator assembly outlet. The vapor
entering the compressor inlet combines with
lubricating oil that is fed to the compressor. The
oil-refrigerant mixture is compressed to raise its
condensing temperature. From the compressor,
the high-temperature, high-pressure mixture flows
to the oil separator, where the oil is removed from
the refrigerant vapor, filtered, and fed back to
the compressor.
If the refrigerant vapor pressure exceeds
250 ± 5 psi in the line downstream from the oil
separator, the high-pressure cutoff switch will
cause the cockpit EQUIP COOLING caution light
to illuminate and the compressor motor solenoid
valve to shut off hydraulic pressure to the
compressor motor, thus shutting down the
compressor. If the cutout switch failed to operate
properly, the relief valve in the compressor
discharge line would relieve the system of pressure
in excess of 325 psi.
Refrigerant vapor from the oil separator next
enters the condenser assembly where ram air
lowers its temperature and changes the vapor to
a liquid. Refrigerant pressure on the high side of
the system is controlled by regulating the amount
of cooling air flowing across the condenser. A
pressure transducer in the high side refrigerant line
provides a signal to a control amplifier, which,
in turn, causes the control actuator and flap to
open and close as necessary to regulate pressure.
The system is calibrated so that the condenser flap
is fully closed when high side pressure is 107± 3
psi; fully opened at 151 ± 3 psi condensing
pressure; and modulates the flap travel for
intermediate pressures within that range.
If the cooling air is inadequate to maintain the
pressure at 151 ± 3 psi with the flap fully open,
the system pressure will exceed the control range.
When the pressure reaches 250 ± 5 psi, the high-
-pressure cutout switch will shut down the vapor
cycle system.
From the condenser assembly, liquid Freon
flows to the receiver in the evaporator group
assembly. The receiver stores surplus refrigerant
and thereby prevents surges in the refrigerant flow
rate. Liquid refrigerant flowing from the receiver
passes through a subcooler and then through a
filter drier, where foreign matter and water
are removed. Before entering the thermostatic
expansion valve, the liquid refrigerant passes
through a sight glass, which provides a visual
3-20
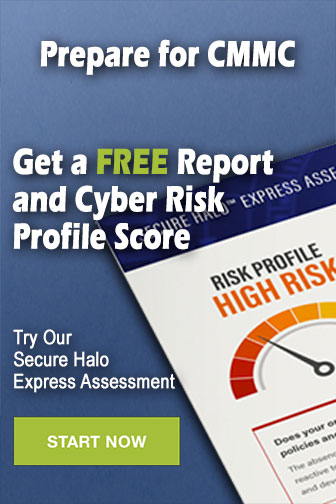