pressure generated in the bulb is transmitted to the
diaphragm in the power section of the valve,
causing the valve pinto open. A decrease in the
temperature of the gas leaving the evaporator will
cause the pressure in the remote bulb to decrease,
and the valve pin will move toward the closed
position.
The superheat spring is designed to control the
amount of superheat in the gas leaving the
evaporator. A vapor is superheated when its
temperature is higher than that necessary to
change it from a liquid to a gas at a certain
pressure. This ensures that the Freon returning
to the compressor is in the gaseous state. The
superheat spring is adjustable and is factory set
to provide approximately 9° of superheat in this
particular vapor cycle system. Superheat setting
is calculated in relation to evaporator size and heat
loads applied; therefore, it should never be
tampered with in the field as serious inefficiencies
will result.
The equalizer port is provided to compensate
for the effect the inherent evaporator pressure
drop has on the superheat setting. The equalizer
senses evaporator discharge pressure and reflects
it back to the power head diaphragm, adjusting
the expansion valve pin position to hold the
desired superheat value.
The purpose of the multioutlet configuration
of the valve is to ensure an even distribution of
the refrigerant in the evaporator.
EVAPORATOR. The evaporator (fig. 3-16)
is a plate fin heat exchanger forming passages for
cooling airflow and for Freon 12 refrigerant. The
evaporator assembly houses a hydraulically driven
fan and a low-temperature cutout switch.
When the vapor cycle system is operating,
refrigerant from the expansion valve flows into
the Freon passages of the evaporator. At the same
time, the hydraulically driven fan is forcing air
from the electronic equipment compartment
across the coils of the evaporator. The
temperature of the air is rather high since it is
affected by being circulated through the electronic
boxes. This air, in passing through the evaporator,
readily gives up its heat to the liquid Freon 12.
The Freon is receptive to the heat exchange and,
in absorbing the heat, a change of state comes
about, changing the Freon from a liquid to a gas
at approximately the same temperature that it was
changed from a gas to a liquid. Since the Freon
compressor is maintaining a constant pressure in
the evaporator, the Freon vaporizes at a
- temperature that causes the air discharging from
the evaporator to the electronic compartment to
be at approximately 40°F. Vapor leaving the
evaporator is also at a temperature of about 40°F.
Attached to the discharge side of the
evaporator is a header duct assembly, bolted to
the perimeter of the evaporator. This header is
used to direct the discharged cooling air to the
various distribution ducts. A set of movable
louvers in the header is designed to act as a shutoff
valve during ground cooling cart operations.
During this time an external cart is attached to
a receptacle on the right-hand side of the fuselage
and feeds to the distribution system for ground
operations, if desired. This air, however, would
also escape in reverse direction through the
evaporator and discharge into the forward
compartment, thereby reducing the airflow to the
electronic equipment. The louvers are actuated by
a single control knob located at the top of the
header duct. The knob is a two-position control
(open and close) and is placarded to explain
operation. To prevent the louvers from being
inadvertently left in the closed position with the
possibility of starving the avionics gear of cooling
air after ground cart operation has been
terminated, an overcenter device is incorporated.
This device will automatically open the louvers
as soon as a pressure is felt on them from the
evaporator fan. The header duct also contains a
discharge air filter, which filters the recirculated
air and also removes the majority of the moisture
(if present) in the cooling air on its way to the
electronic equipment.
COMPRESSOR ASSEMBLY. The purpose
of the compressor assembly (fig. 3-17) is to
evacuate the evaporator, keeping it at a constant
pressure, and also to superheat the Freon vapor
and feed it to the condenser where it is condensed
back into a liquid for reuse. The compressor
houses two intermeshing helical rotors that rotate
in counterrotating directions. This action causes
cool Freon gas to be taken from the evaporator
and compressed. This increases its temperature
and pressure to a value where it may be fed to
the condenser for ambient air to change it back
into a liquid. The compressor controls the pressure
in the evaporator by varying its speed in response
to signals from a suction line pressure switch.
The two intermeshing helical screw-type rotors
are enclosed in a close tolerance housing,
containing an inlet and an outlet port. Since the
rotors mesh, they may be distinguished one from
the other by calling one the male and the other
the female.
The male rotor is directly coupled to, and
driven by, a variable speed hydraulic motor. The
3-24
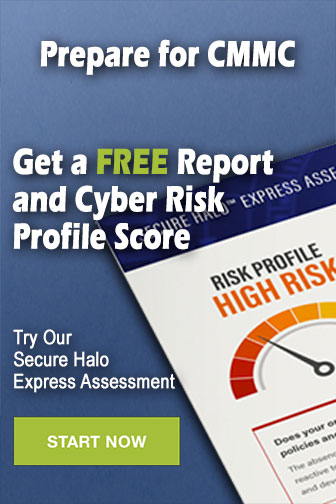