clean oil supply for compressor lubrication. The
filter has a replaceable cellulose fiber element. If
the filter becomes clogged, a bypass device
permits unfiltered oil to circulate through the
compressor when the differential pressure across
the filter is greater than 18 to 22 psi.
When the differential pressure across the filter
is greater than 13.5 to 16.5 psi, the red indicator
at the top of the filter will pop up and remain
extended to provide an indication that the
filter requires replacement prior to becoming
completely clogged, and consequently passing
contaminant oil to the compressor. The oil filter
is designed with an automatic shutoff feature,
which permits removal of the filter element and
bowl without loss of the refrigerant charge.
CONDENSER EJECTOR AIR SHUTOFF
VALVE. The purpose of the condenser ejector
air shutoff valve is to increase airflow across the
condenser during ground operation by discharging
engine bleed air through the ejector assembly. The
valve is pneumatically operated. It is controlled
by a piston through a mechanical linkage and is
spring loaded to the CLOSED position. A
solenoid valve on the actuator chamber side of
the piston acts as a bleed off for the air being fed
from an upstream tap of the valve housing. This
air is fed through the-hollow piston actuator shaft
to the top side of the piston where it is
bled off as long as the solenoid is de-energized.
Energizing the solenoid closes off the actuator
chamber bleed, and pressure builds up. This force
overcomes spring tension and the valve opens.
Any loss of pneumatic or electrical power to the
valve will cause it to assume a closed position.
CHARGING VALVES. There are four
backseating charging valves in the vapor cycle
systemthree in the evaporator group, and one
in the condenser group. The valves are used to
facilitate servicing of the system as one complete
unit or servicing of the evaporator group or
condenser group as individual units. The
condenser and evaporator group assemblies are
equipped with quick-disconnect refrigerant lines
to allow their removal from the aircraft without
a loss of refrigerant.
PURGE VALVES. The refrigerant system
is equipped with two purge valvesone at the
evaporator group assembly high point and the
other on the condenser in the top scoop of the
aircraft. The valves are similar to the charge
valves. They are used to bleed the system, when
required, and for attaching test equipment or the
vacuum pump for system evacuation.
3-26
Maintenance
Maintenance of the vapor cycle ACS, like the
air cycle system, will generally require the joint
efforts of personnel from the AME and the AE
ratings. Malfunctions of the hydraulic motors that
drive the compressor and evaporator fan will
require the services of an AMH.
Operational checkout of the vapor cycle
system can be done in several ways. The AE can
perform an operational check of the electrical
portion of the system using a Cooling System Test
Set, AN/ASM 232 (XN-1), with the engines not
running.
Performing an operational check of the
complete vapor cycle system without the engines
running requires external hydraulic and electrical
power and a source of cool air. The cooled air
is ducted into the condenser scoop inlet to
provide flow through the condenser for con-
densing the Freon. As was stated earlier, this
function is normally done by ram air when
sufficient ram airflow is available or by engine
bleed air leaving the ejector nozzles and creating
a pressure differential that causes sufficient flow
for cooling on the ground when the engines are
running.
The operational check steps as specified in the
applicable MIM should be performed in sequence.
If a trouble occurs during a step, it must be
corrected before proceeding. Isolation of the
trouble can almost always be enhanced by
referring to the step of the troubleshooting table
that corresponds with the step of the operational
checkout where the trouble occurred.
Additional organizational-level maintenance
on the vapor cycle system includes servicing
(adding refrigerant and lubricating oil), leakage
testing and correcting of leaks, and removal and
installation of components.
Intermediate-level maintenance of the
evaporator assembly, the cindenser group
assembly, and the air ejector shutoff valve is
restricted to replacement of parts listed in the
Spares and Repair Parts Data List provided in the
intermediate repair section of the applicable MIM
(Part IV). Special test equipment is required to
bench test most of the vapor cycle components
or assemblies; therefore, not all intermediate-level
activities possess the capability to accomplish such
maintenance.
Since proper servicing of the vapor cycle
system is one of the most important factors
affecting operation, equipment used for servicing
and servicing procedures are given brief coverage
in the following paragraphs.
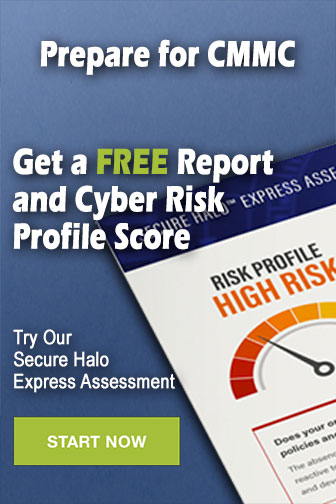