Figure 3-1.Project code breakdown.
States [OUTUS]). After meeting the established time
limit, organizational maintenance activities modify it to
AK0 or cancel it.
For a complete listing of Project codes, refer to the
Operating Procedures Manual, MILSTRIP, Military
Standard Requisitioning and Issue Procedures.
MILSTRAP, Military Standard Transaction Reporting
and Accounting Procedures, NAVSUP Publication
437 (also known as MILSTRIP/MILSTRAP Manual),
and Afloat Supply Procedures, NAVSUP Publication
485.
Force/Activity Designator (FAD) and Priority
Maintenance control assigns a priority to
individual material requisitions according to the
military importance and the urgency of need of the
item. Most fleet operational activities have a FAD II
or III assigned.
Maintenance control in the requisitioning activity
determines the urgency-of-need designator (A, B, or
C). The requisitioning activity uses the FAD and
urgency-of-need to determine the Uniform Material
Movement and issue Priority System (UMMIPS)
priority designator (Arabic numeral) (table 3-1).
NOTE: Abuse of the priority system weakens the
effort that the supply system devotes to units directly
involved in combat.
SUPPLY PROBLEMS AND
SOLUTIONS
The discovery of a leaking valve or an inoperable
radio will cause a problem for your squadron. Think
of the number of people that this one discrepancy will
affect. Once the requirement is passed to material
control, the AK contacts the aviation support division
(ASD) or the supply support center (SSC). If you filled
out the VIDS/MAF correctly, you should receive a
replacement part. If your squadron or activity has a
FAD I designation and the part is available on station,
you should have the replacement part within 1 hour.
Almost all items used by the Navy have NSNs. If
you give an incorrect part number to material control
and the part is not available locally (on the station or
ship), the AK will cross-reference the NSN to the
wrong item, and the order will not meet your
requirements. The most common result of this type of
error is additional downtime (nonflyable status) for the
aircraft you are trying to repair. When the wrong part
arrives at your squadron, you must reorder the part and
use the correct part number. Then, you must wait while
supply processes the order again. Another situation
that might occur when a wrong part number is
cross-referenced to an NSN is the awarding of a
contract to manufacture parts that are not needed.
When repairing aircraft, your paperwork must be
complete and accurate because data from the
paperwork provides usage statistics. The supply
department uses these statistics to justify the need to
stock an item.
3-2
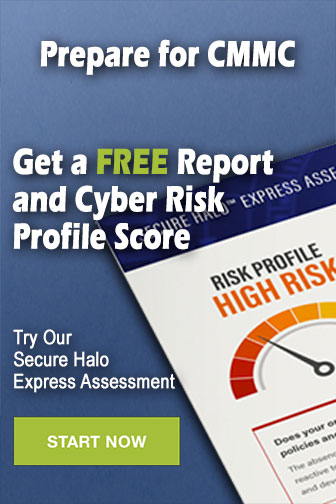