CHAPTER 3
AVIATION SUPPLY
Previous chapters introduced you to some of the
purposes for the various levels of maintenance and the
associated maintenance reports and publications. This
chapter discusses the actions you perform that affect
the logistics support (supply) of your activity.
ORDERING AIRCRAFT
REPLACEMENT PARTS
LEARNING OBJECTIVES: Identify the
purpose and composition of Project/Priority
codes. Define the purpose of Force/Activity
and Urgency of Need Designators. Describe
how the supply department justifies stocking
replenishment items.
The information you provide so readily about your
car cannot be given as easily about aircraft parts.
Therefore, the Navy has shop supervisors and material
specialists, Aviation Storekeepers (AKs), available to
help you identify components and bits and pieces of
components. The AK is the representative of the
aviation supply department, and fills a position similar
to that of the clerk in the automobile parts store.
Remember how you removed the broken water
pump from your car and obtained a replacement for it?
The clerk in the parts store ordered the part by filling
out a form or even more recently, responding to
questions asked by a computer. When you discover a
part on an aircraft that needs replacement, you order
that part on a Visual Information Display
System/Maintenance Action Form (VIDSMAF) or in
Naval Aviation Logistics Command Management
Information System (NALCOMIS).
When entering data on the VIDS/MAF (a 5-part
form), you must use a black ballpoint pen. Press hard
so that all copies are readable, and PRINT LEGIBLY.
Failure to write clearly cannot only cause receipt of
the wrong part, but the AK might order an item that
costs thousands of dollars simply because YOU DID
NOT WRITE A PART NUMBER CLEARLY. There
are many reasons for mistakes. Often: mistakes are as
simple as a transposed part number or NSN. The lack
of a dash number (-1, -2, -3) can cause supply to put
the next higher assembly on order.
When entering a part number, you need to make
sure that the part number is 100-percent correct. DO
NOT GUESS! You should use the publications
available and, if in doubt, ask for help. Not all items
for a particular type of aircraft are interchangeable.
Some examples of differences are different part
numbered items for different models of the same type
of aircraft, and different dash numbers in a part number
to designate which side (left-hand or right-hand) an
item is designed for.
PROJECT AND PRIORITY CODES
Once your work center determines that a part is
required, maintenance control assigns the Project and
Priority codes that material control uses to requisition
the part.
Project Codes
Project codes identify requisitions and related
documents that apply to specific projects or programs.
They are mandatory on Navy requisitions. Their
absence is cause for rejection.
The codes consist of a combination of three codes
(alpha/alpha/numeric) constructed from a matrix that
relates to the type of activity or weapon, the reason,
and the cause/effect (fig. 3-1). Some commonly used
Project codes in an organizational maintenance
activity are as follows:
AK0. Assigned by organizational maintenance
activities only when they requisition material to restore
an aircraft to mission capable (MC) status.
AK7. Assigned by organizational maintenance
activities when they requisition material to return
mission essential subsystems to an operational
condition when an aircraft is in a partial mission capable
(PMC) status,
ZA9. Forced high-time removal items required
for immediate end use on primary mission weapons
systems. The aircraft concerned is within days of
becoming not mission capable supply (NMCS) or
partial mission capable supply (PMCS) due to high time
forced removal of the required item (15 days in CONUS
and 20 days outside continental limits of the United
3-1
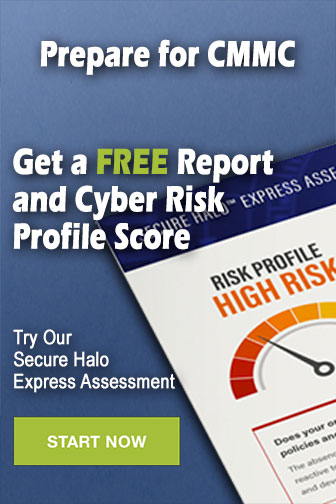