SUPPORT EQUIPMENT (SE)
CORROSION REMOVAL AND
SURFACE PREPARATION
The following text discusses surface preparation
as well as mechanical and chemical paint and
corrosion removal methods for SE. They are listed in
order from the most effective or preferred to the least
effective and not preferred. Each SE maintenance
station develops the procedures for operating surface
preparation equipment according to the applicable
MIMs.
The key to achieving a successful, long-lasting
coating system lies in good bonding between coating
and metallic surfaces of SE. Paint will not bond to a
surface that is poorly prepared. Dirt, oil, grease,
corrosion by-products, moisture, and other
contaminants prevent complete contact between paint
and base metal. In addition, a metallic surface must be
roughened to enable the paint system to bond to the
surface. This roughened or anchor pattern can be
produced by mechanical means or by chemical
etchings.
You should remove corrosion, scale, and old paint
from SE by the least destructive method. Where simple
touch-up painting is required. feather the edges of
existing sound paint with light sanding to provide an
anchor for the touch-up paint.
You must apply the initial paint to SE as soon as
possible following surface preparation. A prolonged
lapse in time between surface preparation and painting
allows corrosion to form on the prepared surface. This
corrosion will cause later coating system failure.
REMOVING DIRT, OIL, AND
GREASE
The first step in surface preparation is the removal
of dirt, salt, lubricants. hydraulic oil, and other surface
contaminants from SE. When grease and oil are
present during abrasive blasting, grinding, or wire
brushing, they will spread out over the treated surface
and disrupt the coating bond. The cleaning method that
you use depends on the type of soil, its extent, and the
available cleaning equipment. Detergent cleaning,
solvent cleaning, emulsifiable solvent cleaning, and
acid cleaning are cleaning or degreasing methods.
Detergents and solvents are highly effective in
attacking and dissolving grease and oil on metal
surfaces of SE. Most solvents can be either applied by
vapor degreasing equipment or by wiping. Solvents
are specially useful for cleaning small parts and
spot-cleaning jobs. Disadvantages of degreasers lie in
their toxicity and flammability. Many solvents are
particularly dangerous when used on oxygen service
equipment.
Emulsifiable solvent (solvents suspended in a
gelatinlike medium) cleaning is an effective cleaning
method for removing heavy oil, grease, wax, and other
contaminants of SE.
Acid cleaning combines the forces of oil solvents
and detergent cleaners in removing grease, oil, light
rust, and other contaminants. The method is useful on
the heavy steel structures of SE where surface etching
is required. This cleaning method requires a thorough
rinse with clean water.
MECHANICAL CORROSION
REMOVAL ON SUPPORT
EQUIPMENT (SE)
Abrasive or grit blasting is the preferred surface
preparation method for many of the components of SE.
Such blasting provides the clean anchor pattern needed
by most coating systems. Wet abrasive blasting is
preferred to dry blasting. Before blasting, disassemble
the components according to the applicable technical
manual. Mask all areas that should not be blasted, such
as tapped holes, key ways, machined surfaces,
reflectors, lights, and gauges.
When using abrasive blasting equipment, you
must wear protective clothing, face shield or safety
goggles, and a respirator.
Wet Abrasive Blasting
Water blasting is a technique that requires
high-pressure producing equipment. It involves the
propelling of water and blasting beads. The water blast
method removes surface chemical contaminants,
deteriorated paint, grease accumulations, oil, and
mastic materials from SE.
NOTE: You must use Sodium Nitrite
MIL-S-24521 during the abrasive process to prevent
flash rusting.
The Hydroblaster or other water blast
machines can be dangerous if not handled properly or
with sufficient safeguards.
4-42
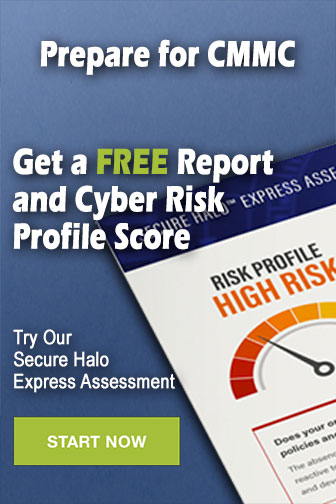