attack, deep pitting, stress corrosion, intergranular,
and galvanic corrosion.
Corrosion of magnesium or its alloys forms white,
powdery, snowlike mounds. The deposits tend to raise
slightly. and the corrosion spreads rapidly. When
magnesium corrosion is detected, it requires
immediate attention or the corrosion will spread
throughout the entire structure. Magnesium corrosion
reprotection involves the maximum removal of
corrosion products, the partial restoration of surface
coatings by chemical treatment, and a reapplication of
protective coatings. After maintenance personnel
clean the surface and strip the paint, (if any,) they break
loose and remove as much of the corrosion products
as possible. They do this by using a pneumatic drill
with an abrasive wheel or a Vacu-Blast Dry Honing
Machine with glass beads. Steel wire brushes.
Carborundum abrasives, or steel-cutting tools
should NOT be used. After corrosion removal,
maintenance personnel treat the surface with
specification MIL-M-3171 (type VI) chemical
treatment solution, as outlined in the NAVAIR
01-1A-509. Then restore the protective paint film.
If extensive removal of corrosion products from a
structural casting was involved, a decision from a
structural engineer may be necessary to evaluate the
adequacy of the structural strength remaining.
Structural repair manuals for the aircraft models
involved usually include tolerance limits for
dimensions of critical structural members. They
should be referred to if any question of safety of flight
is involved.
Copper and Copper Alloys
Copper and its alloys are generally corrosion
resistant, although the products of corrosive attack on
copper are commonly known. Sometimes copper or
copper-alloy surfaces will tarnish to a dull gray-green
color, and the surface may still be smooth. This
discoloration is the result of the formation of a
fine-grained, copper oxide crust called patina. The
patina, in itself, offers good protection for the
underlying metal in ordinary situations. However,
exposure of copper and copper alloys to moisture or
salt spray causes the formation of blue or green salts,
indicating active corrosion. These salts form over the
patina since this crust is not totally moistureproof.
Copper alloys used in aircraft have a cadmium-plated
finish to prevent surface straining and decay.
Copper and copper-based alloys are used in
avionic systems as contacts, springs, connectors,
printed circuit board runs, and wires. Copper and
copper-based alloys (brass and bronze) are resistant to
atmospheric corrosion. However, copper is cathodic to
iron, steel, aluminum, and magnesium when in
electrical contact with these metals.
Maintenance personnel can remove corrosion
products by using a pneumatic drill with an abrasive
wheel or, as an alternate method, a typewriter eraser
(ZZ-E-661. type I or III), depending upon the
situation. Copper and copper alloys used in avionic
equipment are not usually painted.
Cadmium and Zinc
Cadmium is used as a coating to protect the part to
which it is applied. It also provides a compatible
surface when the part is in contact with other materials.
The cadmium plate supplies sacrificial protection to
the underlying metal because of its greater activity.
That is, during the time it is protecting the base metal,
the cadmium is intentionally being consumed. It
functions in the same way that an active magnesium
rod inserted in the water system protects the piping of
a hot-water heater. The cadmium becomes anodic and
is attacked first, leaving the base metal free of
corrosion. Zinc coatings are used for the same purpose,
but to a lesser extent in aircraft. Attack is evident by
white-to-brown-to-black mottling of the cadmium
surfaces. These indications DO NOT indicate decay of
the base metal and should NEVER be removed for
appearance sake alone. Until the characteristic colors
peculiar to corrosion of the base metal appear, no steps
should be taken,
Cadmium is usually used on bolts as a sacrificial
metal to protect the base metal. Zinc is used in
avionic/electronic equipment for the same general
purpose.
Maintenance personne1 remove corrosion
products by rubbing lightly with stainless steel wool,
abrasive impregnated webbing, or 320-grit or finer
aluminum oxide abrasive paper. They do not remove
the undamaged cadmium plate adjacent to the
corroded area; this will reduce the amount of
protection for the underlying base metal. Wire brushes
are not used on cadmium-plated surfaces since they
will remove more plating than corrosion. After
removing corrosion products from cadmium-plated
surfaces, maintenance personnel apply a protective
coating to retard the corrosive attack.
4-38
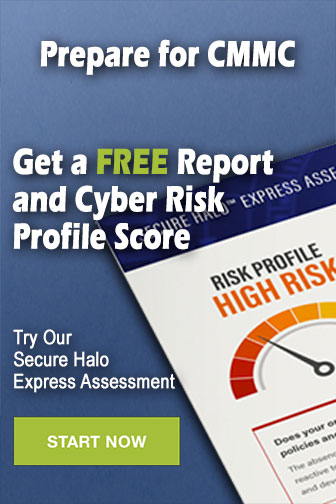