Table 4-2.Corrosion of MetalsNature and Appearance of Corrosion Products
ALLOY
TYPE OF ATTACK TO WHICH
APPEARANCE OF
ALLOY IS SUSCEPTIBLE
CORROSION PRODUCT
Aluminum Alloy Surface pitting, intergranular, White to gray powder.
exfoliation, stress corrosion, fatigue
cracking and fretting.
Titanium Alloy
Highly corrosion resistant. Extended No visible corrosion products at low
or repeated contact with chlorinated temperature. Colored surface oxides
solvents may result in degradation
develop above 700°F.
of the metal's structural properties.
Magnesium Alloy
Highly susceptible to pitting.
White powder snowlike mounds and
white spots on the surface.
Carbon and Low-Alloy Steel
Surface oxidation and pitting,
Reddish-brown oxide (Rust).
surface and intergranular.
Stainless Steel
Crevice/concentration cell
Rough surface; sometimes a red,
(300-400 series)
corrosion; some pitting in marine
brown, or black stain.
environments; corrosion cracking;
intergranular corrosion (300 series)
and surface corrosion (400 series).
Nickel-base Alloy
Generally has good
Green powdery deposit.
(Inconel, Monel)
corrosion-resistant qualities;
susceptible to pitting in seawater.
Copper-base Alloy
Surface and intergranular corrosion.
Blue or blue-green powdery deposit.
Brass, Bronze
Cadmium (protective plating for
Good corrosion resistance. Will
White powdery deposit to
steel)
cause embrittlement if not properly
brown/black mottling of the surface.
applied.
Chromium (wear-resistant plating
Subject to pitting in chloride
Chromium being cathodic to steel,
for steel)
environments.
does not corrode itself, but promotes
rusting of steel where pits occur in
the coating.
Silver
Will tarnish in presence of sulfur.
Brown to black film.
Gold
Highly corrosion resistant.
Deposits cause darkening of
reflective surfaces.
Tin
Subject to whisker growth.
Whiskerlike deposits.
nature and appearance of corrosion products found on
the metals used in aircraft construction.
Iron and Steel
Possibly the best known and the most easily
recognized form of metals corrosion is the familiar
reddish-colored iron rust. When iron and its alloys
corrode, dark iron oxide coatings usually form first.
These coatings, such as heat scale on steel sheet stock,
may protect iron surfaces. However, if enough oxygen
and moisture are present, the iron oxide is soon
converted to hydrated ferric oxide, commonly known
as iron rust. Iron and steel are used in avionic
equipment as component leads, magnetic shields,
transformer cores, racks, and general hardware. Steel
and iron hardware used in aircraft construction is
usually plated with nickel, tin, or cadmium.
Aluminum
Aluminum and its alloys are used many places in
aircraft construction, including ejection seats, chassis
4-35
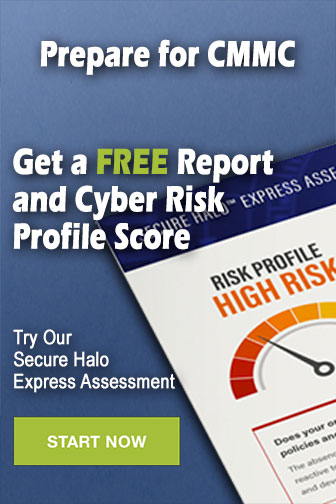