Nickel and Chromium
Alloys
Nickel and chromium alloys are also used as
protective agents in the form of electroplated
coatings. Also, they are used as alloying constituents
with iron in stainless steels, such as the wear
surfaces of aircraft struts. Nickel and chromium
plates protect by forming a physical, noncorrosive
barrier over the steel. Electroplated coatings,
particularly chromium on steel, are slightly porous,
and corrosion eventually starts at these pores or pin
holes unless a supplementary coating is applied and
maintained.
Titanium
Titanium is often used in engine exhaust areas.
Titanium is a highly corrosion-resistant metal.
However, it can greatly accelerate corrosion of
dissimilar metal coupled to it. Insulation between
titanium and other metals is necessary to prevent
dissimilar metal attack on the other metal.
Maintenance personnel must frequently inspect such
areas to make sure that insulation failure has not
allowed corrosion to begin.
Q59.
Q60.
Q61.
Q62.
Q63.
Q64.
Q65.
Q66.
Q67.
Q68.
What publication should you refer to for
information about structural corrosion?
Hydrated ferric oxide is commonly known as
what kind of corrosion?
What are the three types of aluminum surfaces
insofar as corrosion removal is concerned?
How should you remove corrosion from clad
aluminum surfaces?
What is the primary type of aluminum used on
naval aircraft?
What are the approved tools for cleaning
anodized aluminum surfaces?
Who should evaluate any loss of structural
strength in critical areas of an aircraft?
What manual should you refer to for tolerance
limits for dimensions of critical structural
members?
Copper and copper-based alloys are used in
avionic systems for what purpose?
Where is titanium most often used on a
aircraft?
CORROSION REMOVAL AND
TREATMENT
LEARNING OBJECTIVE: Describe the
methods of removing and treating corrosion.
Once corrosion is detected, a specific and
immediate program for corrective treatment is
required. A complete treatment involves paint removal
and cleaning of all corroded areas, removal of
corrosion products, restoration of protective,
surface-treatment films, and immediate application of
protective coating and paint finishes. Each type of
corrosion has its own peculiarities and requires special
treatment. Corrosion should always be removed by the
mildest means available.
CORROSION REMOVAL
Before starting any corrosion removal, you must
conduct an inspection and evaluation of the suspected
area. When you inspect an aircraft or a particular area
of an aircraft for corrosion, you should follow the steps
listed below.
1. Clean the area thoroughly.
2. If an area is suspected of having corrosion,
visually inspect the area by using a magnifying glass.
3. To preclude metal damage, remove paint
chemically from areas suspected of having underlying
hidden corrosion. Use abrasive paint removal
techniques only when corrosive products are observed.
4. After removing the paint, use a magnifying glass
to determine the extent of the damage, especially if there
is evidence of corrosion on critical parts. Corrosion
cracks must be detected as early as possible.
5. Refer to the applicable structural repair manual
(SRM) or MIM for damage limits. Metal loss damage
is accumulative. When assessing corrosion damage,
consider prior metal loss, including areas on the
opposite side of the part. Propellers and helicopter
blades have critical balance requirements. Refer to the
propeller and blade manuals that apply for the
evaluation and repair limits of corrosion, erosion, and
abrasive damage.
After the aircraft or aircraft part has been
inspected, the extent of the corrosion damage must be
correctly evaluated. The severity of corrosion damage
is grouped into the following categories:
Light corrosion. This type of damage is defined as
a protective coating that is scarred or etched by light
4-39
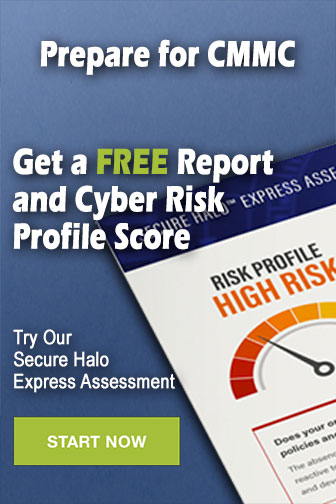