magnesium skin panels, maintenance personnel must
give special attention to these panels during
inspections for corrosion. Some aircraft have steel
fasteners installed through magnesium skin with only
protective finishes under the fastener heads or tapes
over the surface for insulation. In addition, paint
coatings are thin at trimmed edges and comers. These
conditions, coupled with magnesiums sensitivity to
saltwater attack, present a potential corrosion problem
whenever magnesium is used. Therefore, maintenance
personnel must inspect all magnesium skin surfaces
for corrosion, giving special attention to edges, areas
around fasteners, and cracked, chipped, or missing
paint.
The entrance and entrapment of corrosive agents
between the layers of metal cause corrosion of
spot-welded skins. (See figure 4-25.) Some of the
corrosion may be caused originally by fabrication
processes, but its progress to the point of skin bulging
and spot-weld fracture is the direct result of moisture
or salt water working its way in through open gaps and
seams. The first indication of this type of corrosion is
the appearance of corrosion products at the crevices
where the corrosive agents entered. Corrosion may
appear at the external or internal faying (closely
joined) surfaces, but it is usually more prevalent on
external areas. More advanced corrosive attack causes
skin buckling and eventual spot-weld fracture.
Maintenance personnel should detect skin buckling in
its early stages by sighting along spot-welded seams
or by using a straightedge.
Piano-Type Hinges
Figure 4-26 shows the effect of corrosion on the
piano hinges used on aircraft. These are prime spots
for corrosion to develop due to the dissimilar metal
contact between the steel pin and aluminum hinge
tangs. They also natural traps for dirt, salt, and
moisture. When used on access doors and plates, these
hinges tend to freeze in place because they are opened
only during periodic inspections. While inspecting for
corrosion of these hinges, maintenance personnel
should lubricate the hinge and move the hinge back
and forth several times to ensure complete penetration
of the lubricant.
RECOGNIZING AND ELIMINATING
CORROSION
One of the problems you will have as a
maintenance crew member is recognizing and
combating corrosion on different materials. The
following paragraphs include brief descriptions of
typical corrosion product characteristics that are
normally found on the materials used in aircraft
construction. Also included are the normal procedures
for their elimination and prevention. Treating internal
corrosion of equipment requires a trained technician,
and is normally accomplished at the intermediate-
maintenance level. The materials found in avionic
equipment, such as gold, silver, tin, solder, and copper
alloys, are prone to many forms of corrosion. The
treatment for corrosion involving these materials can
be found in NAVAIR 16-l-540. When in-depth
information is needed about structural corrosion, refer
to NAVAIR 01-1A-509. Table 4-2 identifies the
Figure 4-25.Spot-welded skin corrosion points.
4-34
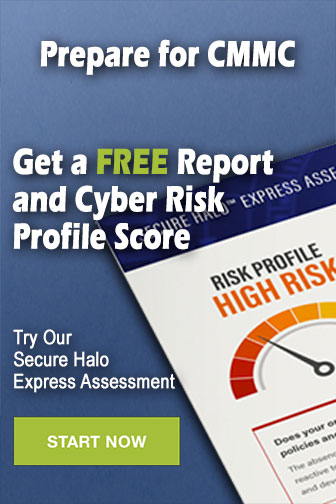