205.166
Figure 4-27.Aluminum corrosion products.
removal of the protective clad layer and exposure of
the more susceptible, but stronger, aluminum alloy
base.
If there is any superficial corrosion present, you
should treat it by wiping down the surface with an
inhibitive material, such as the Chemical Surface
Films for Aluminum Alloy, available under
specification MIL-C-81706.
Anodized Aluminum Surfaces. Nonclad
aluminum alloys are the primary type of aluminum
used on naval aircraft. Anodizing is the most common
surface treatment of nonclad aluminum alloy surfaces.
In anodizing aluminum alloys, the alloy sheet or
casting is the positive pole in an electrolytic bath in
which an oxidizing agent produces an aluminum oxide
film on the metal surface. This aluminum oxide is
naturally protective, and anodizing merely increases
the thickness and density of the natural oxide film.
When this coating is damaged in service, it can only
be partially restored by chemical surface treatments.
Therefore, when processing anodized surfaces,
including corrosion removal, you should avoid
destruction of the oxide film.
Aluminum wool (nylon webbing impregnated
with aluminum oxide abrasive) or fiber bristle brushes
are the approved tools for cleaning anodized surfaces.
The use of steel wool, steel wire brushes, or harsh
abrasive materials on aluminum surfaces is prohibited.
A buffed or wire brush finish produced by any means
is also prohibited. Otherwise, anodized surfaces are
treated in much the same manner as other aluminum
finishes.
Exfoliated Surfaces. As previously described,
exfoliation is a separation along the grain boundaries
of metal and is caused by intergranular corrosion.
More severe procedures must be used when
intergranular corrosion is present. All corrosion
products and visible delaminated metal layers must be
removed by mechanical means to determine the extent
of destruction and to evaluate the remaining structural
strength of the component. Maintenance personnel use
metal scrapers, rotary tiles, and other tools to assure
that all corrosion products are removed and that only
structurally sound aluminum remains. Maintenance
personnel should inspect the area with a 5- to 10-power
magnifying glass or use a dye penetrant to determine
if all unsound metal and corrosion products have been
removed. When all corrosion products have been
removed, maintenance personnel should blend or
smooth out any rough edges, even if it involves the
removal of more metal. Grinding, where required, is
best done by using abrasive nylon wheels into which
tiny particles of aluminum oxide abrasives have been
impregnated. Chemical treatment of exposed surfaces
is applied in the same manner as any other aluminum
surface. An aeronautical engineer should evaluate any
loss of structural strength in critical areas. This is
particularly true if the damage exceeds the permissible
limits established in the structural repair manual for
the aircraft model involved.
Magnesium
Magnesium and its alloys have limited use in
aircraft structural construction. However, they are
used extensively throughout avionic systems as
antennas, structures, chassis, supports, and frames.
Magnesium, without a protective coating, is highly
susceptible to corrosion when exposed to marine
environments. Magnesium forms a strong anodic
galvanic cell with every other metal and is ALWAYS
the one attacked. Magnesium is subject to direct acid
4-37
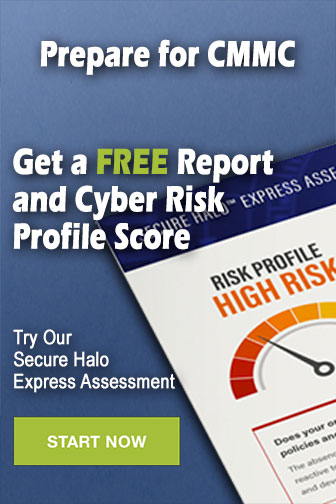