II activity can submit priority 2, 5, and 12 requisitions,
depending on the urgency of requirement as related to
mission readiness. A FAD III activity would submit
priority 3, 6, and 13 requisitions for corresponding
requirements.
Project codes are assigned to identify requisitions
and related documents applicable to specific projects or
programs and are mandatory entries on all requisitions.
Project/Priority codes are discussed in more detail
in chapter 3 and in OPNAVINST 4790.2.
AWAITING PARTS
VALIDATION
LEARNING OBJECTIVE: Recognize the
purpose for performing awaiting parts
validations.
Validation of AWP items, using the AWP list
provided by the aviation support division (ASD), is
performed jointly with the AWP unit in supply at least
weekly. AWP validation ensures all parts on order by
a particular command are still required and all required
parts are still on order. This validation also points out
possible cannibalization actions, which can reduce the
number of AWP components.
Q35.
What action is taken at least weekly to ensure all
parts on order are still required and all required
parts are still on order?
WORKLOAD PRIORITY
ASSIGNMENT
LEARNING OBJECTIVE: Identify the
different priorities assigned to I-level
maintenance workloads.
Production control, working with the component
control section (CCS) and the aeronautical material
screening unit (AMSU) of the supply department, will
set workload priorities based on the following:
Priority 1. Support of non-mission capable (NMC)
or partial-mission capable (PMC) aircraft; NMCS or
PMCS items, based on a valid outstanding requisition
held by supply; expeditious repair (EXREP); or work
requests causing NMC or PMS conditions on an
aircraft will be assigned priority 1. Priority 1 is also
assigned to activities within 30 days of deployment.
Priority 2. Repair of critical local repair cycle
assets (LRCAs) and SE. This priority is also assigned
to O-level maintenance work stoppage requirements.
7-21
Priority 3. Repair of non-critical LRCAs and SE
and repair or manufacture of material for non-fixed
allowance stock.
Priority 4. Processing of salvaged material and
nonaeronautical work.
These priorities may be adjusted by the IMA
maintenance and supply officers as necessary to meet
local support requirements and operation conditions.
Q36.
Production control works with what other work
centers in the supply department to set workload
priorities?
EQUIPMENT STATUS REPORTS
The successful operation of an IMA from
production control depends on knowledge. As
mentioned before, production control is the nerve
center of the IMA. If a supported activity needs
anything in the way of support from the I-level
activity, it will contact production control. For
production control to have its finger on the pulse of the
entire department, it needs to be continuously updated
on equipment status. From the status of support
equipment to avionics test benches, the production
control chief MUST know at a glance what assets he
has available to work with.
Equipment status reports normally provide this
information. These status reports are normally furnished
to production control at the beginning of each work day
and sometimes at the beginning of each shift.
Equipment status reports provide important
information, such as how many NCPP-105 air start
units are on board, and how many of them are up (fully
operational) or how many are down, what maintenance
is required to make them ready for use, and when they
are anticipated to be ready for use. Almost every
division in the IMA provides these reports to the
production control officer, with information pertinent
to the successful operation of an IMA.
SUMMARY
This chapter touched only briefly on the
responsibilities of maintenance and production
control. It is by no means an all inclusive recipe book
for successful operation of either work center. Both
maintenance control at the O-level and production
control at the I-level are very important and busy
management offices. Communication and teamwork
are key factors in managing a successful work center.
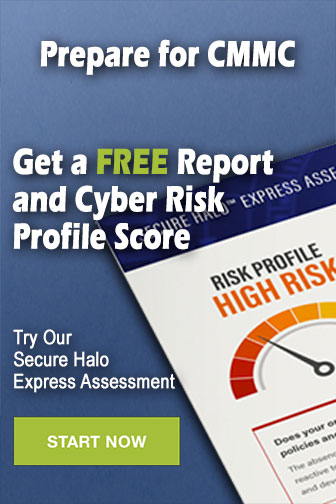