aircraft or in ready room issue. These inspections
are done at the organizational level of mainte-
nance by personnel assigned to the aviators
equipment branch. The date of these inspections
and inspectors signature are recorded in the
inspection section of the Aviation Crew Systems
History Card.
To perform the turnaround/daily/preflight/
postflight/transfer or special inspections, visually
inspect the following:
1. Cushion for secure attachment, rips,
tears, and loose or grayed stitching.
2. Release handle for proper seating and
corrosion.
3. Oxygen gauge for FULL indication.
4. Emergency oxygen lanyard coupling as-
sembly for spring security.
5. Emergency oxygen lanyard for proper in-
stallation and corrosion.
6. Manual emergency oxygen release for
condition and security of attachment.
7. Container assembly for cracks, breaks,
and other obvious damage.
8. Harness assemblies for loose or frayed
webbing, stitching, and cracked or broken
hardware.
9. Lapbelt release assembly for loose or
missing screws and corrosion.
10. Beacon actuator indicator for bent shaft,
hairpin cotter for elongation and corrosion.
11. Secure attachment of beacon automatic
actuation lanyard (if installed).
12. Seal decal for secure attachment, tears,
or rips. If the seal decal is damaged, the RSSK
must be reclosed by IMA.
13. Condition of oxygen hose and secure
attachment to kit. If repair procedure has been
performed on the oxygen hose assembly, check
external wiring for secure attachment.
14. For the S-3A aircraft, secure attachment
of externally mounted electrical cable assembly
to oxygen hose assembly.
If any parts must be replaced, note that similar
parts from kits made by different manufacturers
are not interchangeable. Attempts to substitute
one manufacturers part for another may cause
the kit to malfunction. Make sure the parts and
assembly lists are for the proper kit when servicing
a kit, or ordering replacement components for it.
If discrepancies are found or suspected, main-
tenance control must be notified.
Survival kit assemblies that do not pass in-
spection and cannot be repaired in the aircraft
must be removed and replaced by Ready for Issue
(RFI) survival kits. Non-RFI survival kits are
forwarded to the nearest maintenance activity
having repair capability.
ACCEPTANCE/PHASED/SDLM
INSPECTIONS
The acceptance inspection is performed when
the survival kit is placed into service. When a
survival kit is an aircraft inventory item, the
acceptance inventory inspection and packing
serves as the acceptance inspection. In this case,
the records concerning the RSSK must be
examined. Phased/SDLM inspection cycle of a
survival kit corresponds to the aircraft
phased/SDLM maintenance inspection cycle as
scheduled by the Planned Maintenance System.
In no case should the phased interval exceed 225
days.
Visual Inspection
This inspection will be performed prior to the
functional check of the kit. Visually check the kit
for the following:
1. The cushion for rips, tears, and general
condition.
2. The release handle for wear, corrosion, and
damage.
3. The manual emergency oxygen release
handle (green ring) for damage and security of
attachment.
4. The upper and lower container for cracks,
corrosion, and security of hardware.
5. Webbing for loose or frayed stitching and
security of attachment.
6. The lapbelt release assembly for loose or
missing screws and corrosion.
7. Swaged balls on cable assemblies for
security of attachment. The swaged ball pull test
is performed during the acceptance inspection
only.
Swaged Ball Pull Test
To check the swaged ball attachment to cable
assemblies, you will need a nylon cord, Type II
scale (at least 100-pound capacity). Perform the
pull test as follows:
1. Remove four screws and cover from as-
sembly.
2. Push actuating lever down (fig. 7-4).
7-4
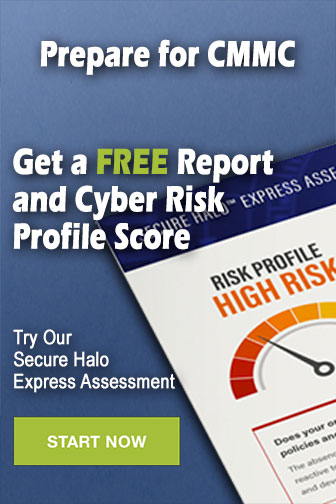