CHAPTER 3
NES-12 PERSONNEL PARACHUTE SYSTEM
Learning Objective: Upon completion of this chapter, you will be able to
understand the theory of operation and perform a speciaL inspection on the
NES-12 parachute assembly.
The modern high-performance aircraft used
by the Navy today make extreme demands of
emergency escape devices. The most critical time
for ejection from an aircraft is at low altitudes
especially on takeoffs and landings. The ultimate
goal in seat performance (to which engineers have
been working) is one that safely ejects the
occupant at zero airspeed and at zero altitude, at
low altitudes under a high speed, or under other
adverse altitude conditions. The system discussed
in this chapter gives the aircrewman a zero
airspeed and a zero altitude ejection system.
The 1G series ejection seats separate from the
aircrewman by means of a rocket that forcibly
propels the seat away from the crew member after
ejection.
After the aircrew member ejects from the
aircraft, a static line on the outside of the
container pulls the external pilot chute from its
pocket. The sequence of events shown in figure
3-1 commences. This static line is also attached
to the arming cable for the automatic parachute
ripcord release. The external pilot chute is
intended to cause the parachute to open more
rapidly, especially at low altitudes or during
ground-level ejection. It is of a tristage design and
functions as follows: At speeds from 0 to 90
knots, it will inflate to full diameter; at speeds
between 90 to 250 knots, the full diameter will
reduce to 24 inches; and at speeds in excess of 250
knots, it will invert, but its effective drag will be
sufficient to stabilize the aircrew member during
free fall and also aid in the extraction of the main
canopy during deployment.
At a preset altitude, the automatic ripcord
release fires, pulling the ripcord pins from the
locking cones, allowing the spring opening bands
to open the container. The internal pilot parachute
springs from the container and fills with air during
this operation. The external pilot chute release
assembly frees the shear link cable when the
container opens.
The internal pilot parachute causes the main
canopy to be pulled from the container, followed
by the suspension lines. A short piece of 18-pound
nylon tape is used to momentarily shorten the
canopys effective length during low-speed
ejection, which, in turn, promotes more positive
opening characteristics. Just prior to full
suspension line stretch, the ballistic spreading un
fires, forcing the suspension lines out at the skirt
hem. This rapidly opens the canopy and allows
it to fill with air faster. Ties on the connector links
break as load is applied, allowing the risers to be
pulled from the container.
NOTE: If the spreading gun fails to fire,
the slugs separate from the gun assembly
at full suspension line stretch, allowing the
canopy to open aerodynamically.
The aircrew member hangs suspended in his
harness from the quick-release shoulder fittings
during descent. The parachute has the four-line
release system that was described previously. By
manually actuating this system, the aircrewman
is able to maneuver the parachute to a less
hazardous landing site and to reduce oscillation
during descent. Upon landing, the canopy and
suspension lines can be disengaged from the
integrated torso suit by means of the quick-release
shoulder fittings.
NOTE: After the incorporation of Aircrew
System Change 446, the seawater activated
release system provides an automatic
backup method of releasing the risers after
the crew member makes a seawater entry.
3-1
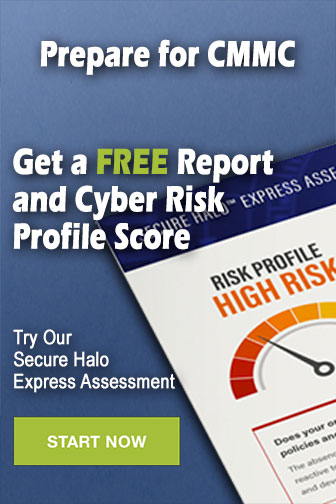