converter supply flow control valve V-9 controls
the flow of oxygen from the liquid oxygen
converter through the heat exchanger HE-1 to the
buildup and flow valve V-10, and then to the
adapter fixture.
Linear Flow Elements
There are four linear flow elements. Each
measures a different flow rate in liters per minute
(LPM). By using a hose assembly connected from
NIP-5 (converter supply outlet connection) to the
correct one of the linear flow elements (NIP-1 for
0-00.25 LPM, NIP-2 for 0-1.0 LPM, NIP-3 for
0-50 LPM, or NIP-4 for 0-150 LPM), and turning
the flowmeter selector valve, you can measure
leakage from an item under test.
Liquid Oxygen Quantity Gauge
Capacitor-Type Tester
The liquid oxygen quantity gauge capacitor-
type tester is located on the upper front panel of
the test stand and operates on 115 Vat, 400-cycle
current. It is used to measure capacitance and
electrical insulation of the capacitance probe.
Flow of Oxygen
As you turn on the supply of gas, it flows into
the test stand through a special bulkhead fitting
BF-1 (fig. 11-4), and it is indicated on the 0-3,000
psig pressure gauge PG-3. It then flows to the
adjustable pressure regulator R-1. The regulator
is preset to deliver 160 psig to the remainder of
the test stand through oxygen supply valve V-6.
Oxygen supply valve V-6, a needle-type valve,
admits oxygen to the adapter fixture and controls
oxygen pressure to an item under test. From the
adapter fixture, the test gas is routed to the follow-
ing valves, gauges, and disconnects:
Test gas enters the bell jar bottom coupling
C-1. Your test item is also attached to this
coupling. From C-1 it flows to the needle metering
valve V-2, which allows the flow to continue to
a test pressure gauge PG-1.
NOTE: When opening valve V-2, you must
close valve V-10. This prevents oxygen
from entering the converter side of the test
stand.
The test pressure gauge PG-1 indicates the
pressure applied to the item under test. The
oxygen flow also goes from the adapter fixture
to the differential pressure gauge shutoff valve
V-8. This valve prevents pressure from being
admitted to the high side of the differential
pressure gauge DF-1 when the gauge is not being
used. Another flow from the adapter fixture is
to the system bleed valve V-5. This valve is a
needle-type valve, and it is used to bleed the
pressure from the test stand. On every test stand
you will find a safety valve. In this case, we have
a relief valve V-4 that prevents excessive pressure
buildup in the test stand. The valve is leaktight
at 160 psig, and is set to relieve at 180 psig.
MAINTENANCE
Maintaining and preparing the test stand for
use is divided into five separate tasks: installation,
visual inspection, correction card preparation,
calibration, and leak testing. These tasks, fully
described in the following paragraphs, are out-
lined briefly below:
1. Installation includes selecting a suitable
space, mounting, connecting to a suitable power
supply, and an oxygen source.
2. The visual inspection is performed to
ensure the test stand has not been damaged during
shipment and installation.
3. Correction/calibration cards (fig. 11-6)
provide an easy reference upon which indicated
flows and pressures are recorded. Actual
mandatory flows and pressures are taken from
NAVAIR 17-15BC-20 and are prerecorded on the
correction/calibration cards. The actual LPM
flow must be converted to the indicated inches of
H2O flow and to millimeter (mm) flow by using
the applicable flowmeter calibration graphs. This
conversion is performed by the metrology calibra-
tion team.
NOTE: Additional actual pressures and
flows have been added to the correction
cards in figure 11-6. Addition of these
pressures and flows reflect required actual
pressures and flows needed to bench test
RSSK kits and all models of LOX
converters now in service.
4. Periodic leakage tests are conducted on the
accessories section, bell jar assembly, and the
entire test stand.
5. Calibration of the test stand is required to
be performed prior to use. Calibration procedures
are performed at 6-month intervals by the onsite
metrology calibration team. Additional calibra-
tions are not required.
11-16
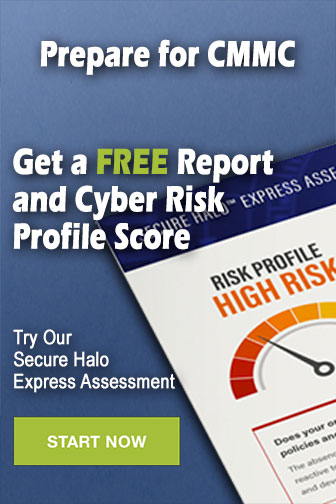