The MMP should be prepared and distributed by
the 25th day of the month prior to the month to which it
applies. For example, the MMP for April should be
distributed by the 25th of March. The MMP should be
distributed to maintenance supervisors within the
activity and to the supporting IMA and the station/ship
supply officer.
Although the MMCO has the responsibility for the
preparation of the MMP, AZs who are assigned to
maintenance control or maintenance administration
usually prepare a rough draft of the plan for the
MMCOs approval. Production work centers provide
some input for the MMP, however other information,
such as scheduled inspection due dates, may be
extracted directly from NALCOMIS. After the MMP is
completed, the finished product is submitted to the MO
for signature.
Intermediate Maintenance Activity (IMA)
Monthly Maintenance Plan
The MMP is published by an IMA for use by its
production divisions and activities that it supports. The
IMA officer holds a monthly meeting. This meeting
provides the planning and coordination to improve the
overall maintenance program. Representatives of the
maintenance and supply departments of supported
activities attend this meeting.
The organizational maintenance representatives
who attend this meeting discuss the quantity and types
of support required. The discussion also includes the
contents of organizational maintenance activity (OMA)
monthly maintenance plans. Squadron representatives
should discuss all factors that affect the anticipated
IMA workload. This meeting is a valuable tool in
planning the monthly maintenance schedule. The
following are minimum information that should be
included in the IMA monthly maintenance plan:
A projected schedule of items to be inducted for
check and test from supported squadrons and the
supply activity.
Anticipated changes in the operational
commitments of supported activities.
A schedule of technical training.
A schedule of maintenance requirements for
shop-installed SE.
Other known or anticipated factors that affect
the production effort of the IMA.
All known technical directives incorporation
requirements.
A current list of QARs, CDQARs, and CDIs.
Forced removal (high-time) components.
Weapons department inputs. These inputs
should include the following: a projected
schedule of armament weapons support
equipment (AWSE) inspection, items that
require test and check, anticipated receipts or
transfers, all known weapons support equipment
(WSE) TD incorporation requirements, and
identification of known or anticipated AWSE
end items or components that will be returned to
the IMA for maintenance beyond the capability
of the weapons department.
The IMA MMP should be completed and
distributed not later than the last day of the month prior
to the month to which it applies. For example, an IMA
MMP for April should be distributed not later than the
31st day of March.
WORK REQUESTS
Frequently, OMAs and IMAs request the help of
higher levels of maintenance to complete work that is
beyond their capability of maintenance due either to the
lack of facilities, expertise, or authorization. Refer to
the NALCOMIS End Users Manual and the NAMP for
detailed documentation procedures for work requests.
A brief discussion of each type of work request follows.
MAF Work Request (OPNAV 4790/60)
The maintenance action form (MAF) work request
is used by a supported maintenance or supply activity to
request work or assistance from a supporting IMA for
work that is beyond the requesting maintenance or
supply activitys capability. The MAF work request,
shown in figure 5-20, is used for, but not limited to, the
following requests:
To request check, test, and service of items that
are removed from an aircraft, equipment, or SE
for scheduled maintenance when the requested
work is beyond the capability of the requesting
activity
NOTE: Work requests for items that are
removed for check, test, service, and local manufacture
or fabrication must be approved and signed by the
requesting activitys maintenance control supervisor
5-29
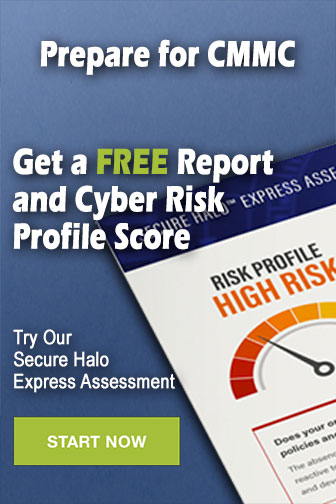