. Responsible senior enlisted personnel are
positioned to observe the flow of material and watch for
possible material loss. The most experienced personnel
should be placed at possible bottlenecks and in areas
normally associated with the receipt of sensitive items
such as pilferable, hazardous, and classified material.
Personnel should not be allowed to begin receipt
processing under any conditions that encourage
carelessness. When necessary, material receipt can be
processed upon completion of the replenishment and
after stores are located in secure spaces.
TYPES OF STORES ANTICIPATED. The
number of receiving stations that must be manned
depends largely on the amount and types of stores
anticipated. Normally 2 or 3 days before the scheduled
replenishment, the transferring ship notifies the
receiving ship as to the nature and amount of stores to
be transferred. The figures given are, in most cases,
rough estimates that can be used for planning purposes.
A safe rule of thumb is to plan for a one-third excess
over the tonnage expected, and planners should assume
that at least some of every category of material will be
received. A replenishment plan must be flexible to
make sure that its use is not destroyed by sudden,
unexpected changes in quantities and type of stores
received. Personnel must be available to handle all
types of material at one time.
It is especially important to know the quantity and
type of dangerous and semisafe material to be received.
Adequate flammable storage space must be available to
accommodate such material. Special procedures
should be established so that this type of material can
be taken directly from the receiving station to the paint
or flammable storerooms and not be allowed to
accumulate on deck.
Each type of stores received is handled in a different
manner and should be directed to different storage
locations. Plans for the replenishment must include the
consideration of peculiar characteristics of all types of
incoming stores. Some of the most important aspects
of handling each category of material are discussed in
the following paragraphs.
Aviation Stores. Aviation material received
during UNREP normally involves several different
small items packed together in large boxes at the
shipping point.
Shipping containers obviously
containing only one item need not be opened, but are
directed to the proper staging area or storeroom at once.
Items shipped as multipacks should be opened,
checked, sorted, and forwarded to storerooms (or
special receiving areas) as soon as possible. Normally,
it is not advisable to move multipacks into storerooms
simply to save time in clearing the deck. The AK in
charge of flight clothing should be on hand during the
sorting to take charge of his or her material.
Sorting and checking of aviation stores should be
performed where manual handling can be minimized,
and where the necessarily slower activity does not
interfere with the rest of the replenishment operations.
Debris from breaking open boxes should be cleared at
once and disposed of according to local instructions.
General Stores. General stores received during
UNREP include bulky materials such as rags, toilet
paper, brooms, swabs, and paint. Many of these items
are difficult to handle with mechanical equipment.
Sorting and checking of this type of material should be
done under the supervision of a senior Storekeeper.
Dry Provisions. Dry provisions represent a large
portion of any replenishment. This category of material
is the easiest to handle and sort. Most of these items are
shipped in sturdy fiberboard cartons that are designed
to move on conveyors easily and stack neatly on pallets.
They are normally light enough to be handled by one
person. Checking and sorting of this type material is
required in all cases by senior Mess Management
Specialists.
Particular care must be exercised in
handling items in bags such as flour and sugar.
Fresh Provisions. Fresh provisions are
somewhat difficult to handle and to move to the reefers.
This is particularly true on ships where reefers are
located in areas where access is difficult. The process
of moving fresh provisions below decks can become
bogged down and create a bottleneck.
Qualified personnel from the medical department
should be on hand to inspect fresh produce and survey
fruits and vegetables that did not pass inspection. Mess
Management Specialists should be stationed in such
places as necessary to detect spoiled produce and save
manhours used in handling the commodities.
Frozen Provisions. The most important
requirement when moving frozen provisions is speed.
Frozen products must be moved into the freezer
immediately upon receipt. When the ship is operating
in hot climates, the steel decks become very hot and
frozen items thaw rapidly (partially or completely) and
make them unsafe for consumption. Checking and
sorting of this type receipt should be done by Mess
Management Specialists.
3-15
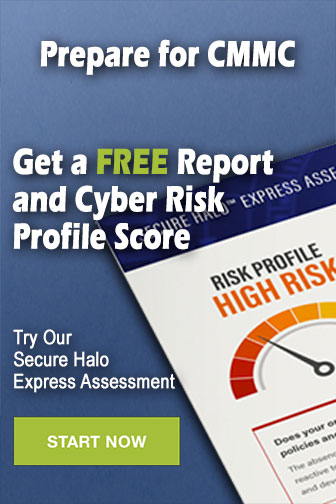