item inside the container and must remain with the item
until it is through processing.
DISPOSITION OF MTIS. After screening and
identification processes have determined that the
material is in any one of the four categories listed above,
the material and documents are distributed as described
in the following paragraphs.
Material for transfer to DRMO fall into one of three
categories. They are items that need inventory manager
disposal authority, items that do not need disposal
authority, or scrap and waste. Material determined to
be in the category for transfer to DRMO is forwarded
to the disposal or shipping section for further action or
delivered directly to DRMO. The document used for
transferring material to DRMO must contain a Disposal
Authority Code. Disposal authority code M is assigned
for transfers authorized by the item manager. Code N
is assigned for material that is not reportable by virtue
of an exclusion to the MRP of NAVSUP P-437 or other
specific criteria such as extended dollar value or
condition limitations on excess reporting and are duly
authorized to be transferred to DRMO. Code N is
assigned for material that has been reported to inventory
manager/inventory control point according to the
Material Returns Program described in NAVSUP P-437
and are excess to authorized retention levels. Code N
is used when disposal/action complies with
Service/Agency Instructions. The items transferred to
DRMO must be accompanied by a minimum of three
copies of DD Form 1348-1. Personnel accepting the
material should receipt for the items and forward one
copy of the signed receipt document to the transferring
activity or the bearer. When DRMO acknowledges
receipt of material, the shipping activity should prepare
and submit a shipping status (DI AS3), with distribution
code 9 in record position 54, to the Defense
Reutilization and Marketing Service (DRMS). Refer to
Appendix B of NAVSUP P-437 for the format in
preparing document identifier AS3.
Material for stock storage. Material determined to
be in the category for storage is forwarded to the
appropriate storage location with a minimum of two
copies of the DD Form 1348-1.
PROCESSING REPAIRABLE MATERIAL.
Each shore activity supporting fleet units or dependent
activities should establish a specific location for turning
in repairable MTIS items.
The shore activity should furnish additional
packaging when the need is indicated on the DD Form
1348-1, or when the condition of the containers shows
an obvious lack of protection and additional packaging
is required. When additional packaging is not requited,
material turned in for transshipment should be
forwarded directly to the transportation section for
processing.
MTR items take precedence over all other MTIS,
provided they are properly identified, Critical items
turned in on a priority 03 (transportation priority 1), and
may be identified as RED STRIPE, must be processed
immediately upon receipt. Items of short supply
turned-in on priority 06, and maybe identified as BLUE
STRIPE, must be processed immediately as resources
permit. If transshipment is required, premium
transportation, including air shipment, is authorized for
RED STRIPE and BLUE STRIPE material. process
material shipments according to Military Standard
Transportation and Movement Procedures, DOD
4500.32-R.
Screening by consignee activity to verify accuracy
of identification or consignment of documented
turn-ins should be performed selectively as required
according to NAVSUPINST 4419.2. Screening to
verify adequacy of packaging should be limited to a
visual inspection to determine if the DD Form 1348-1
indicates a need for additional packaging (block GG
marked Packaging Required) or if the condition of the
material or container indicates an obvious need for
additional packaging. MTR material received without
documentation or with inadequate documentation
should be forwarded to the screening section for further
processing. Discrepancies noted should be reported
according to NAVSUPINST 4440.179 or
NAVSUPINST 4610.33.
MATERIAL RECEIPT AFLOAT
The material receipt process afloat involves the
identification, storage, issue, and recording of all
material previously requisitioned or purchased and
received by the activity. As an integral part of the
supply receipt process, all material received must be
properly identified, stored (if the material is for stock),
issued (if the material is for DTO), and recorded in the
stock records through SUADPS-RTin a timely fashion.
The receiving process is apart of the supply support
operation cycle.
Receipt processing interfaces with
other supply functions such as procurement,
expenditure, and inventory management. The
3-11
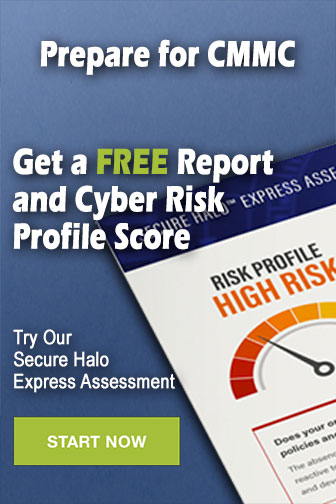