CHAPTER 3
MATERIAL RECEIPTS AND EXPENDITURES
The term receipt refers to material and services
received for stock and direct turnover (DTO). The term
expenditure refers to transactions involving either an
issue, transfer, cash sale, or survey of material. This
chapter contains information about procedures
involving material receipts and expenditures.
The two most important management functions of
any supply department organization are material receipt
and expenditure. These functions are part of the daily
routine operations in the supply environment. The
prompt and accurate processing of material receipts and
expenditures greatly contributes to effective supply
operations.
A properly planned layout of the work area and a
smooth flow of documents and material make an
effective receiving operation.
Material issue is the most common method used for
expending items of supply stock. In general, the issue
transaction for a consumable item will result in an
expenditure to an end-use fund. These funds are then
used to requisition replacement items for stock.
However, the procedures for expending aviation depot
level repairable (AVDLR) items are different. When
processing AVDLR, the expenditure will be processed
only when the turn-in is beyond the repair capability of
the supporting aviation maintenance activity. In this
case, the retrograde is shipped off and the stock
replenishment requisition is submitted to the supply
source.
As a senior AK, you must know the procedures for
processing receipts and expenditures because you will
perform supervisory duties, either directly or indirectly,
in all phases of these tasks. To properly perform these
duties, both ashore and afloat, you should be familiar
with your organization and its duties. You must also
know the following information:
receiving operations,
types of receipt,
methods of delivery,
format of various forms used in receipts and
expenditures,
3-1
l
l
l
filing system,
receipt preparation, inspection, and verification,
and
disposition of material and documents.
The procedures for processing receipts and
expenditures vary depending upon the systems or labor-
saving devices used.
The availability of computer .
systems such as the Shipboard Uniform Automated
Data Processing System-Real Time (SUADPS-RT)
saves processing time. The aviation community in the
Navy uses the Naval Aviation Logistics Command
Management Information System (NALCOMIS). The
Naval Integrated Storage, Tracking, and Retrieval
Systems (NISTARS) and Integrated Barcode System
(IBS) are used for receipt processing. Although
automated systems are being used, there are times when
transactions must be processed manually. You must
know the contingency procedures used for processing
receipts and expenditures manually to continue
operating and prevent backlog.
MATERIAL RECEIPT
Material receipt is the gaining of possession of an
item of Navy property through acceptance of physical
custody. Receiving activities must have full control of
the material after receipt and before it is forwarded to
its ultimate destination. It is estimated that losses that
occur during this cycle range from 40 to 70 percent of
total material losses in the supply system. The control
procedures must include the following processes:
l
l
l
Identification of quantity received
Source and date of receipt
The unit to which physical custody was
transferred at the completion of the Receiving
process and the date on which the received
material was released
Material may be received from several
transportation sources such as the U.S. Postal Service,
commercial or government air freight, commercial
trucking firms, the United Parcel Service (UPS), vendor
deliveries, commercial or government water freight,
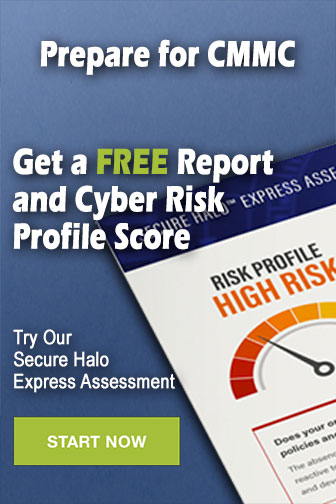