P-545. Automated activities can process offload items
by using the mechanized offload procedures in
SUADPS-RT. Stock control personnel can also use
SUADPS-RT to process offload items manually by
using the proper option and computer screens.
Aviation Fuel
Aviation ships record inventories of aviation fuel in
the same manner as Navy stock account (NSA) items.
Stock control maintains the material data information
for aviation fuel in the stock records. Stock control use
the stock record for recording all transactions, such as
receipts, issues, and transfers. For activities using
SUADPS-RT, refer to the support procedures for
processing the transactions.
PROCUREMENT. The aviation fuels officer is
responsible for determining fuel requirements. The
aviation fuels officer advises the supply officer of the
quantity and desired delivery date of stock
replenishment. Stock control prepares requisitions for
aviation fuels by using the off-line procedures. Refer to
paragraph 3404 of NAVSUP P-485 for additional
information about requisitioning procedures.
RECEIPTS. Stock control processes receipt
transactions according to the local procedures.
Differences between the quantity invoiced and quantity
received are processed as gain or loss by inventory.
EXPENDITURES. Aviation fuel expenditures
include issue to aviation units, issue to ships propulsion,
offload, or cash sales.
Issues and transfers of fuels to aviation units will
result to a charge to the units OPTAR. This will appear
as a charge to the proper flight operations (FLTOPS)
fired code of the squadron or unit.
Issues of aviation fuel to ships propulsion will be
charged to the fleet commanders open allotment.
Aviation fuels offloaded to Navy shore activities are
documented on DD Form 1149 and processed as other
supply officer (OSO) transfers.
Aviation fuel provided to Air Force planes or
activities or other DOD aircraft will be processed as cash
sale transactions.
INVENTORY ADJUSTMENTS. Aviation fuel
lost by other than receipt adjustment should be
documented by a survey. Some causes of fuel losses
include stripping, flushing, spills, or contamination,
Stock control will prepare a separate survey each time
a loss of fuel is determined. At the end of each month,
stock control sends a message report of fuel inventory
adjustments to SPCC. This report is required monthly
to include negative reports. SPCC uses these reports to
review and combine gains, losses, and surveys on a
quarterly basis. SPCC will process the result as charge
or credit to an allotment provided by
commander for the net gains or losses.
PHYSICAL INVENTORIES
the type
Physical inventories are a prerequisite to efficient
inventory control. The primary goal of a physical
inventory is to ensure that the quantity reflected in
records agrees with the quantity in location. The
computer program can produce inventory count cards
or listings to aid in accomplishing the inventory
schedules on almost any basis desired. Some of the
options available are inventory by storeroom,
cognizance symbol, money value, or shelf life. To get
the inventory aid, stock control submits a request to the
system coordinator for the specific option desired.
Based on the stock control request, the system
coordinator prepares the necessary documentation to get
the desired inventory output.
Automated activities may use the Logistics
Applications Marking and Reading Symbols
(LOGMARS) Inventory Module. This is an integrated
program designed for shipboard scheduled or
unscheduled physical inventory functions. The
LOGMARS inventory program uses the barcode reader
to gather inventory data. These data are uploaded to the
host computer system. The LOGMARS inventory
program provides two inventory options. They are the
NIIN and location inventory options. The NIIN
inventory option allows the user to inventory all
locations on file for selected items of stock. The location
inventory option allows users to inventory all or selected
group of stock within a specified location or range of
locations. Refer to the LOGMARS User's Guide for
detailed procedures about the system.
BULKHEAD-TO-BULKHEAD
INVENTORIES
Bulkhead-to-bulkhead inventories are physical
counts of all stock material within ships or specific
storerooms. A bulkhead-to-bulkhead inventory of a
ships entire stock of repair parts is usually taken during
a Supply Operations Assistance Program/Integrated
Logistics Overhaul (SOAP/ILO). A bulkhead-to-
bulkhead inventory of a specific storeroom is taken for
the following reasons:
10-9
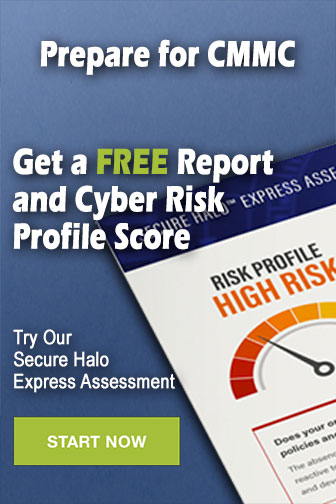